Kaos came with an electrical system that I wanted to completely replace. After lot of design and prototyping, version 1 of the new system has been in place for 6 months and is working extremely well.
The Existing System
The original system was a pretty typical setup that needed some updates. There were OK groups of batteries for the main engine start bank, generator, and thruster. They were being charged in weird ways, and the thruster batteries were as far as possible from the actual thruster, but they worked reasonably well.
There was a house bank and an inverter bank, both using the same style of GC2 6 volt flooded batteries. The house bank was 6x of these located in the engine room, and were responsible for all DC 12 volt loads - lights, pumps, instruments, and also some heavy loads including the windlass and dinghy davit. The inverter bank was in the lazarette and consisted of 8x of the same GC2 6 volt batteries connected directly to a Magnum MS2812 inverter that powered all outlets throughout the boat, the refrigerator, and the microwave.
In total, I had the following capacity:
- House bank - 705 amp hours, 353 usable
- Inverter bank - 940 amp hours, 470 usable
Those are pretty typical numbers for this type of system, but really low for a boat this size, and definitely not the capacity I want for the future. The biggest problem with the existing system was age. The house batteries were from 2015 and well past their usable lifetime.
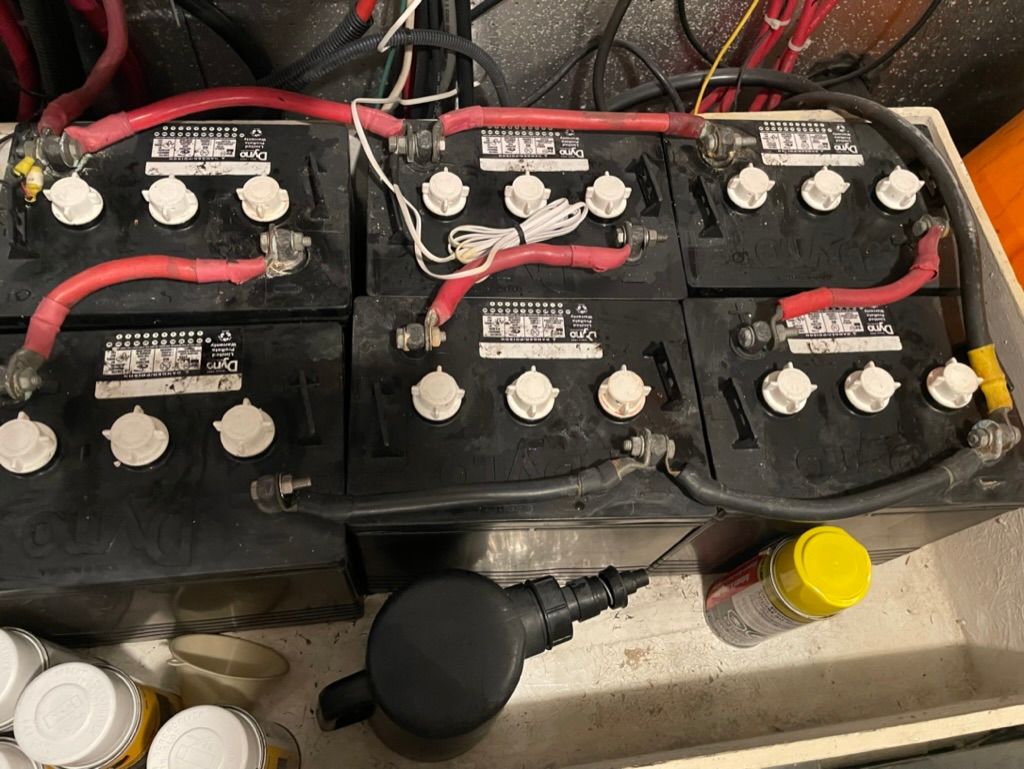
Within the first week of owning the boat, I determined the house bank was actually worse off than originally thought. It couldn't even last a 2 hour inaugural cruise from Anacortes to Friday Harbor without dipping below 11 volts and causing issues. I ended up having to run the generator the whole time underway - not a long term plan.
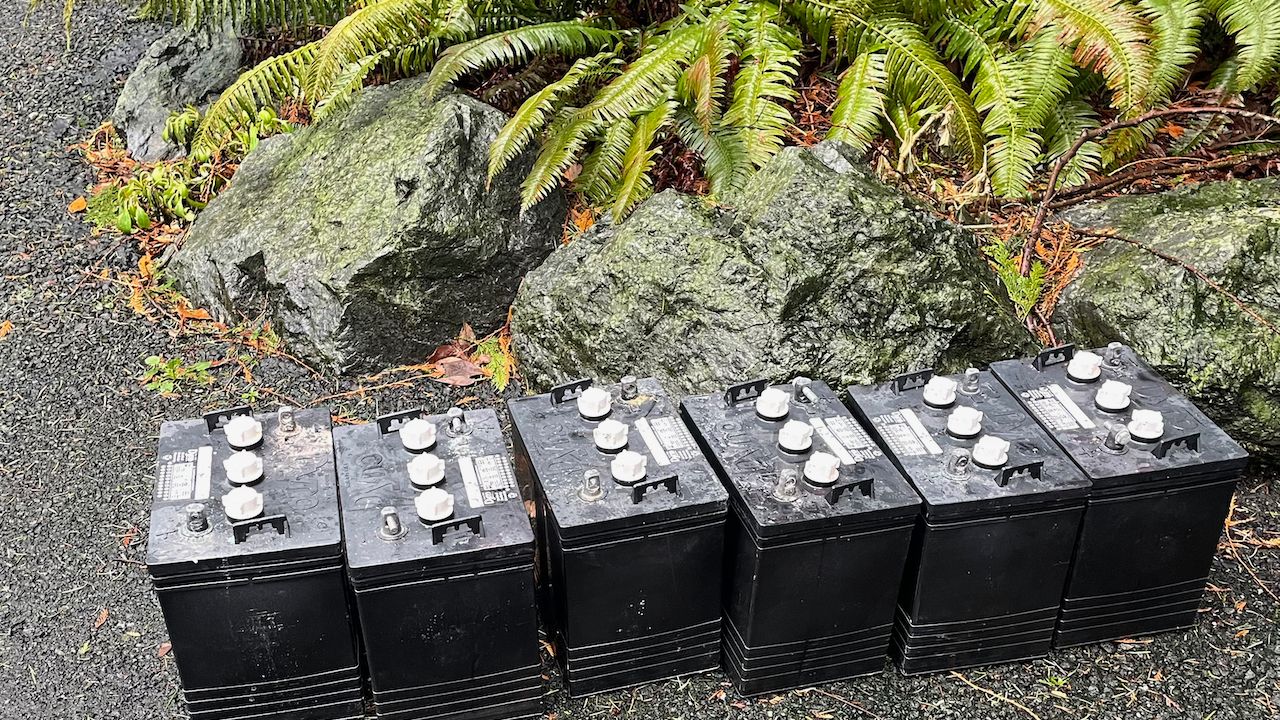
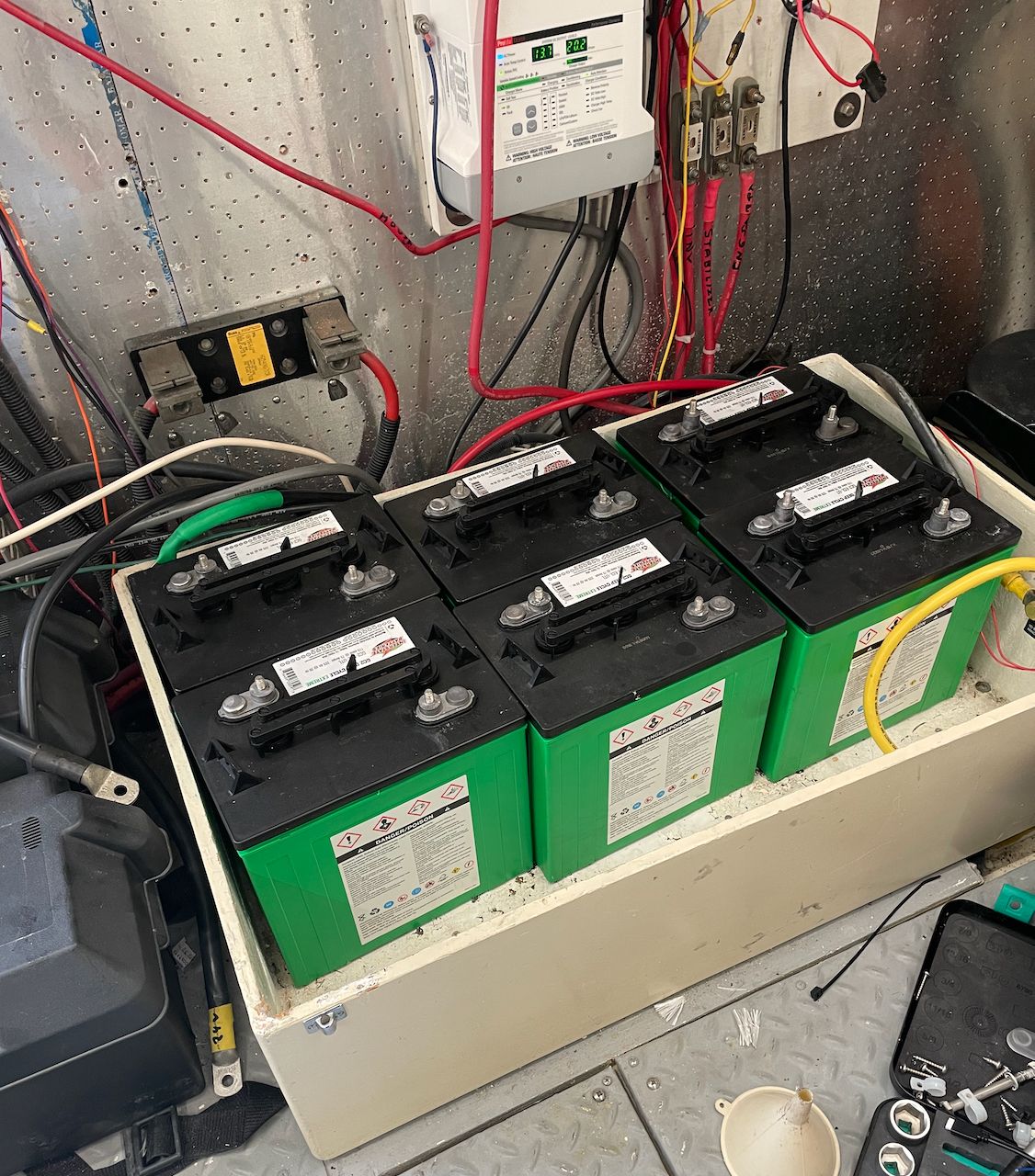
Old and new flooded batteries.
While in Friday Harbor, I ended up having to replace all 6 of the house batteries in order to continue using the boat reliably for the next couple of months while I finished the design.
Even with new batteries, this sort of configuration is not optimal - having the house and inverter banks separated is a throwback to when boats had limited or no inverter power, and one was added. It adds inefficiencies and more complexity. Kaos also had an automatic charging relay (ACR) that was installed to combine the house and inverter bank which allowed for slightly better balancing, but really confusing charging results.
With this setup, my average generator run time was between 4-5 hours per day, sometimes more depending on what was going on.
I also had reverse engineered the AC panel and shore power connections and found some concerning things. Open grounds, weird wiring for the 50 amp 240 volt input connector, etc. After a lot of review, I wanted to simplify the way the panel was setup as much as possible, and re-do the wiring for the shore power side of the world to make sure it was more reliable and safe.
New System Goals
The main goals with the new system were:
- Single bank for inverter / house loads
- More amp hour capacity
- Shorter generator run time / faster charging
- More inverter power / all AC loads on inverter (stretch goal)
- Better visibility and control
48 Volt Discovery
One of the most interesting things I investigated was using 48 volt batteries as the core of the system. I had been watching the market and various products that had become available since my previous boat Rendezvous LiFePO4 power system, and had liked the idea of having a more dense, efficient battery bank at a higher voltage.
I spent a lot of time on forums, talking to experts, and even deeper dives with boaters that already have 48 volt systems. This included folks like Peter Kennedy at PKYS, a Victron expert and a very accomplished ABYC Marine Electrician, and boater David de Regt on Highwind who had installed a 48 volt system aboard his boat, and a handful of others.
What I found was a good core of products that work with 48 volt systems, but key pieces that are a challenge in some way. For example, there are only a handful of 48 volt alternators and the cheapest ones I found were in the $2000-3000 range.
Other challenges included converting 48 volts to 12 volts, which I needed for my existing DC system. Finding solutions to do this was the biggest challenge in the design, and proved to be almost impossible without relying on brand new technology that was even too bleeding edge for me, or using other solutions which weren't meant to be used for this sort of system.
Finding batteries was a bit of a challenge as well. None of the mainline marine vendors produce a 48 volt battery, which means either combining a couple of 24 volt batteries, or choosing less mainstream options.
Finally, there are challenges with ABYC and other regulations around 48 volts, although some have improved in recent months. Many of the regulations end their approvals at 48 volts, which was an issue for any system since the charging rates for a 48 volt system are actually higher.
Ultimately, I decided that going for a 48 volt system was too risky for Kaos at this point in time. Maybe in the future!
24 Volt System
I settled on a basic design around a 24 volt battery bank with 24 volt inverters. Using 24 volts instead of 12 creates a problem, and solves another.
The problem it creates is that the rest of the boat's DC system is still 12 volts, and I'm not changing all of that. There are some solutions to that, which are covered in my design further below.
The problem this solves is the cabling and charging challenges found with 12 volt LiFePO4 systems of any decent size. This is a common issue I see in designs particularly around cabling. A common cabling size used for big battery banks and inverters is 4/0 AWG. ABYC says that a single conductor, used in an engine room, at 105 degrees C, not bundled, sheathed, or in conduit has a max ampacity of 378.3 amps. That same size wire in a group of three, sheathed, bundled, or in conduit drops to 264.8 amps.
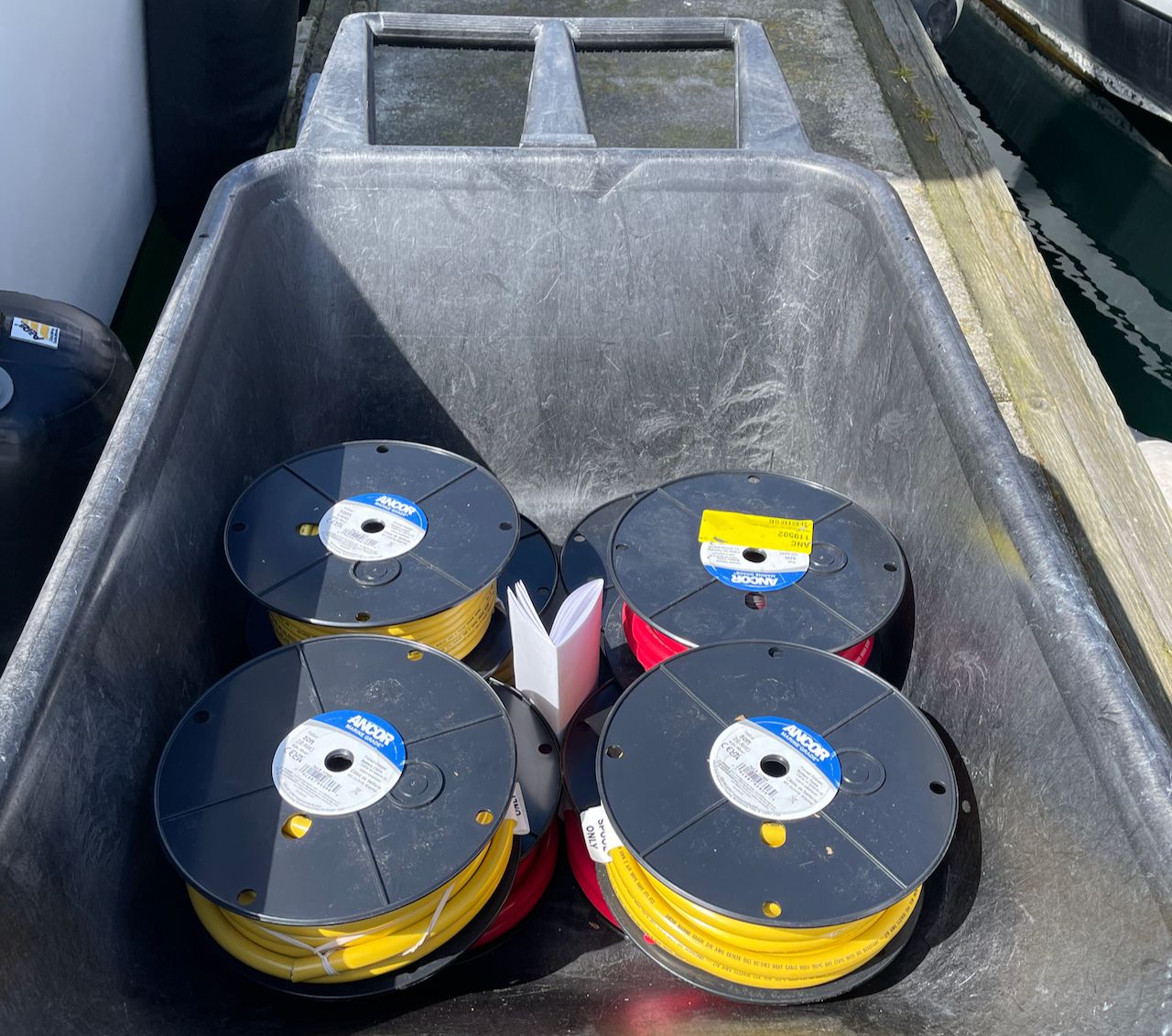
A common design using dual Victron Quattro inverters is a great way to illustrate the challenges here.
- 12 volt Victron Quattro 5000W 120V AC inverter - max charge per unit - 200 amps. 2x units = 400 amps.
- 24 volt Victron Quattro 5000W 120V AC inverter - max charge per unit - 120 amps. 2x units = 240 amps.
Depending on how you wire the 12 volt system, you could end up needing two 4/0 AWG conductors to carry 400 amps safely, and if you do that, they could technically need to be individually fused - again, depending on the design. If they are individually fused, you could also need to somehow disable the inverter/link/wiring if one fuse fails, otherwise you'd have the full load on one wire.
This is just an example with an inverter - if you throw alternators or other charging devices in the mix, you could end up with a lot more to deal with, and trying to do that at 12 volts is becoming more and more challenging.
24 volts just makes a lot more sense from the cabling and charging world, and there are a lot of products and solutions available for this voltage.
Vendor Choice
While I have been a Victron convert for the last couple of boats (Rendezvous & Grace), I try to stay current on what all of the other vendors in the space are doing. I had worked on many MasterVolt systems in the distant past, and really like the quality of their equipment, but they have a gap with monitoring and management compared to Victron. Outback was the other vendor I spent a lot of time reviewing this time around, and have loved their rock-solid inverters for years. They also have pretty terrible management, and were missing other features that I wanted around redundancy, so they weren't a choice.
Most of my experience with customers and my own boats in the last 5 years has been around Victron. They have a lot of great features, but they design things like engineers, for engineers. That's not necessarily a bad thing, but it can mean a lot of work to figure out moderately complex configurations, and unclear documentation about how things work.
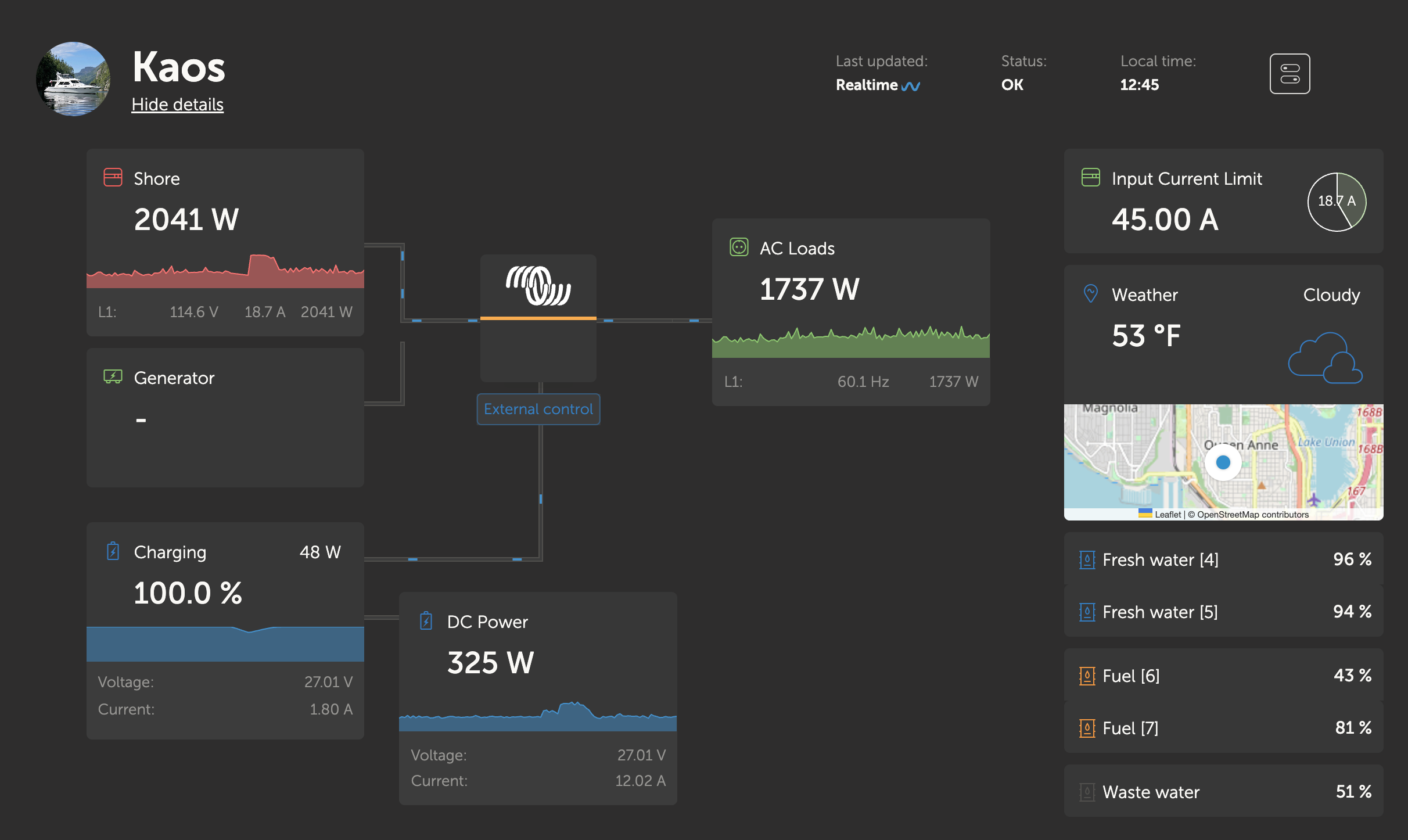
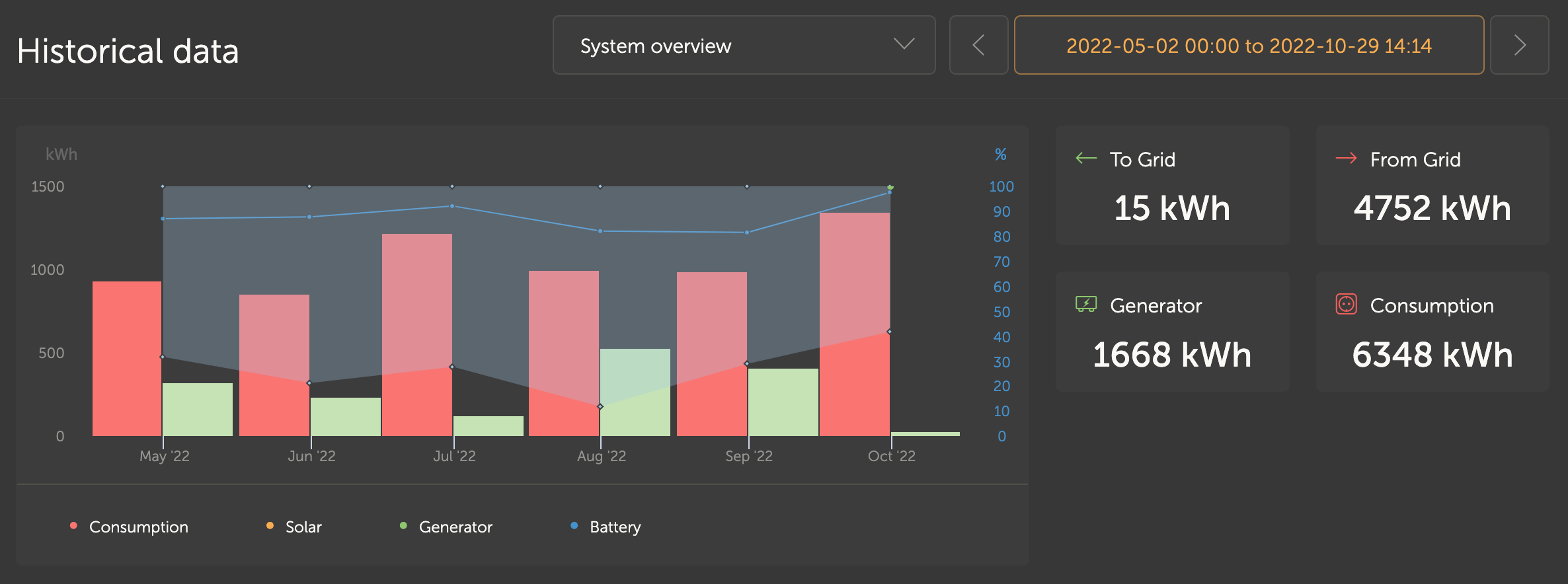
Nevertheless, I had become addicted to features like Power Assist, the online VRM portal, and the lovely GX-series screens and data that you can see about your power system. So Victron it was....
Drop-In vs. Normal LiFePO4
On Rendezvous, I used Battle Born GC2 batteries, a drop-in LiFePO4 battery. On Grace, I used Victron's LiFePO4 batteries. The difference between these types of batteries has been a topic of discussion before on my site, as well as many other places, and have their pros and cons.
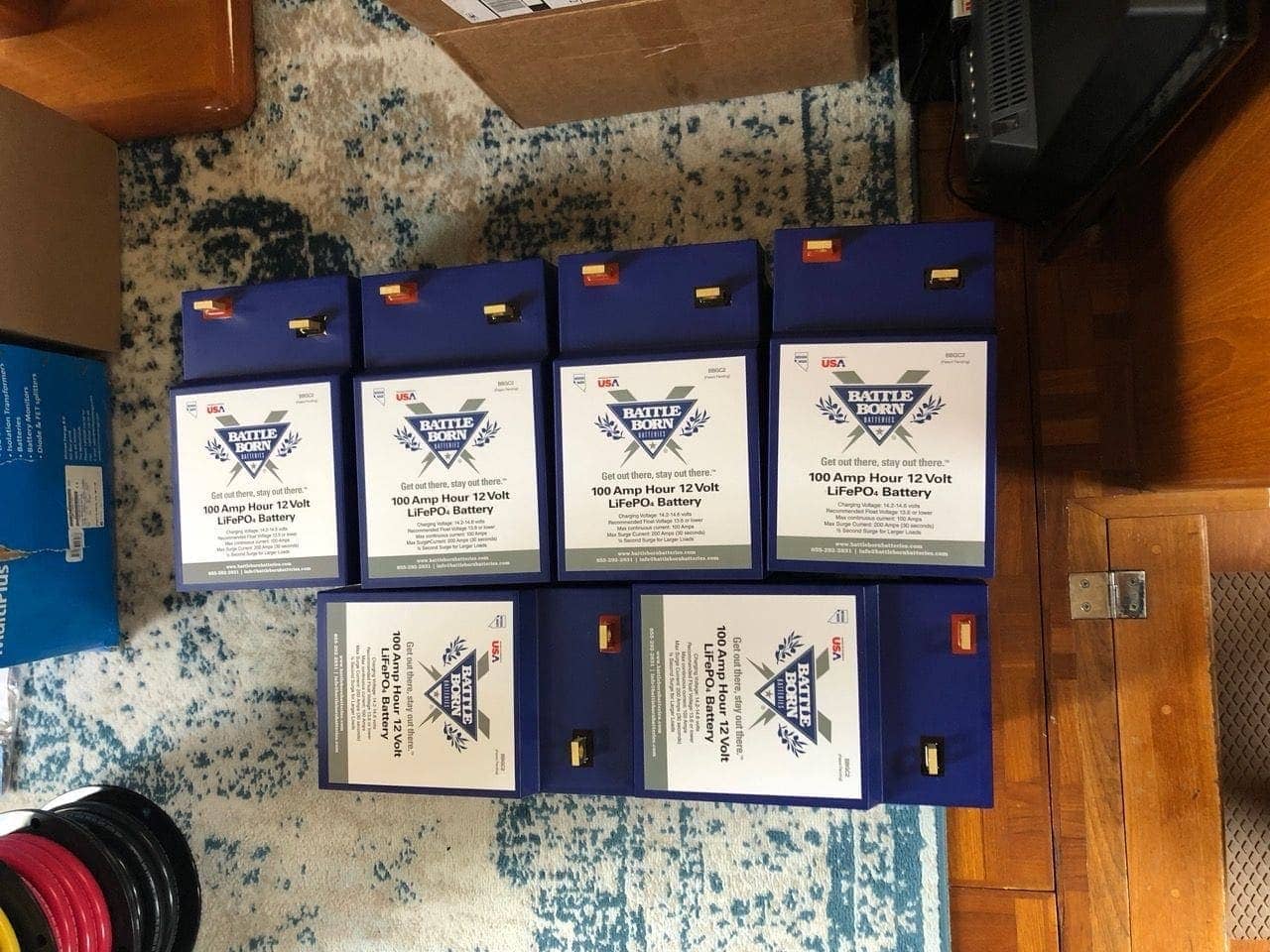
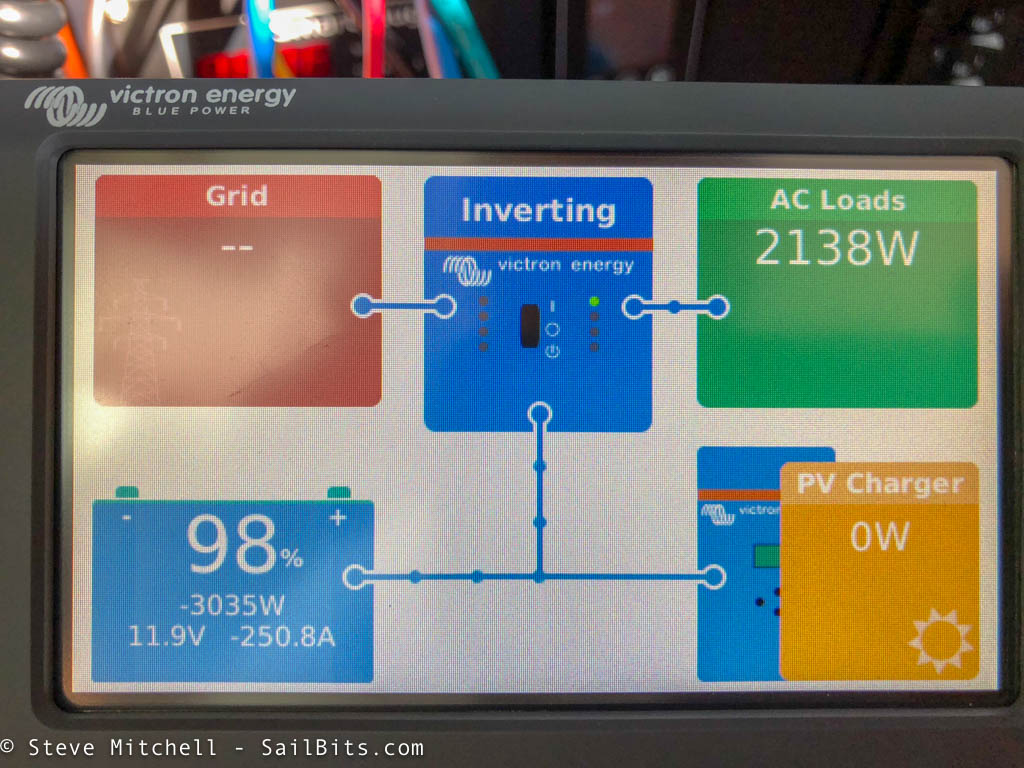
I really liked the simplicity that the Battle Born batteries provided, but there was little visibility into what was going on with each battery. The form factors are also pretty limited - G31, GC2, and 8D - and I wanted a bit more choice.
A lot of the traditional LiFePO4 batteries from Victron, Mastervolt, and others are not as energy dense as I would like, and are really expensive.
However, around the beginning of 2022, Victron released a new "-a" battery that matched my needs, and with some serious discounts, they were comparable to drop-in pricing. Additionally, they were a better form factor and weight, so I was sold on using these for my design.
Design
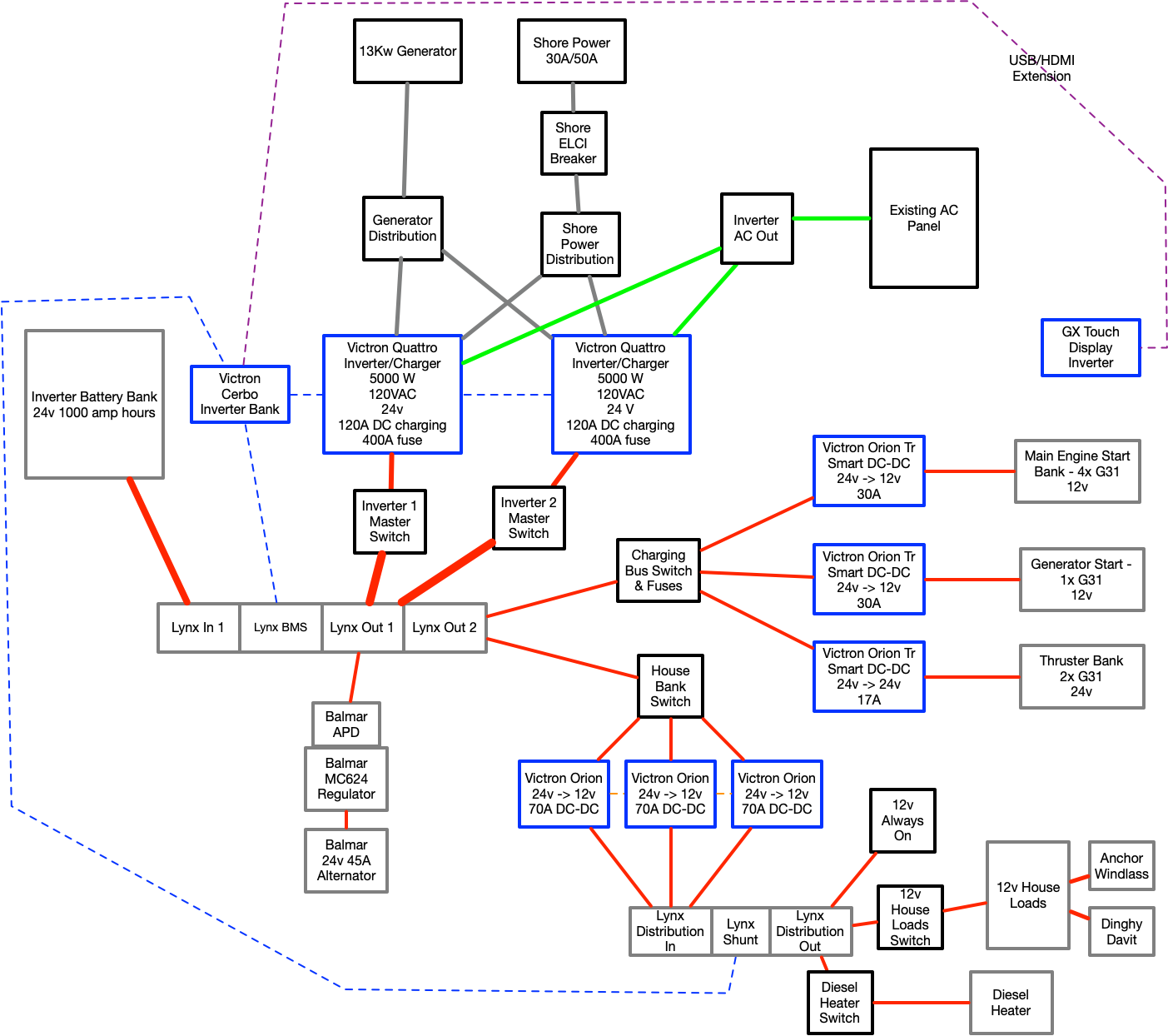
The final design took a while to settle on both during the design phase, and during implementation. I'm a huge fan of iterative design, and always prefer refining a design or a system over time to make sure it is as efficient and effective as possible. In the case of this system, I made a few changes while installing things after being able to test some of the configurations in the real world.
I'll try to break apart the major components of the system below and describe the installation and design.
House Batteries
Victron released a newer version of their 24 volt, 200 amp hour LiFePO4 battery around the time I was doing my installation. They are the LFP-Smart 25.6/200-a model and are quite a bit nicer than the previous versions.
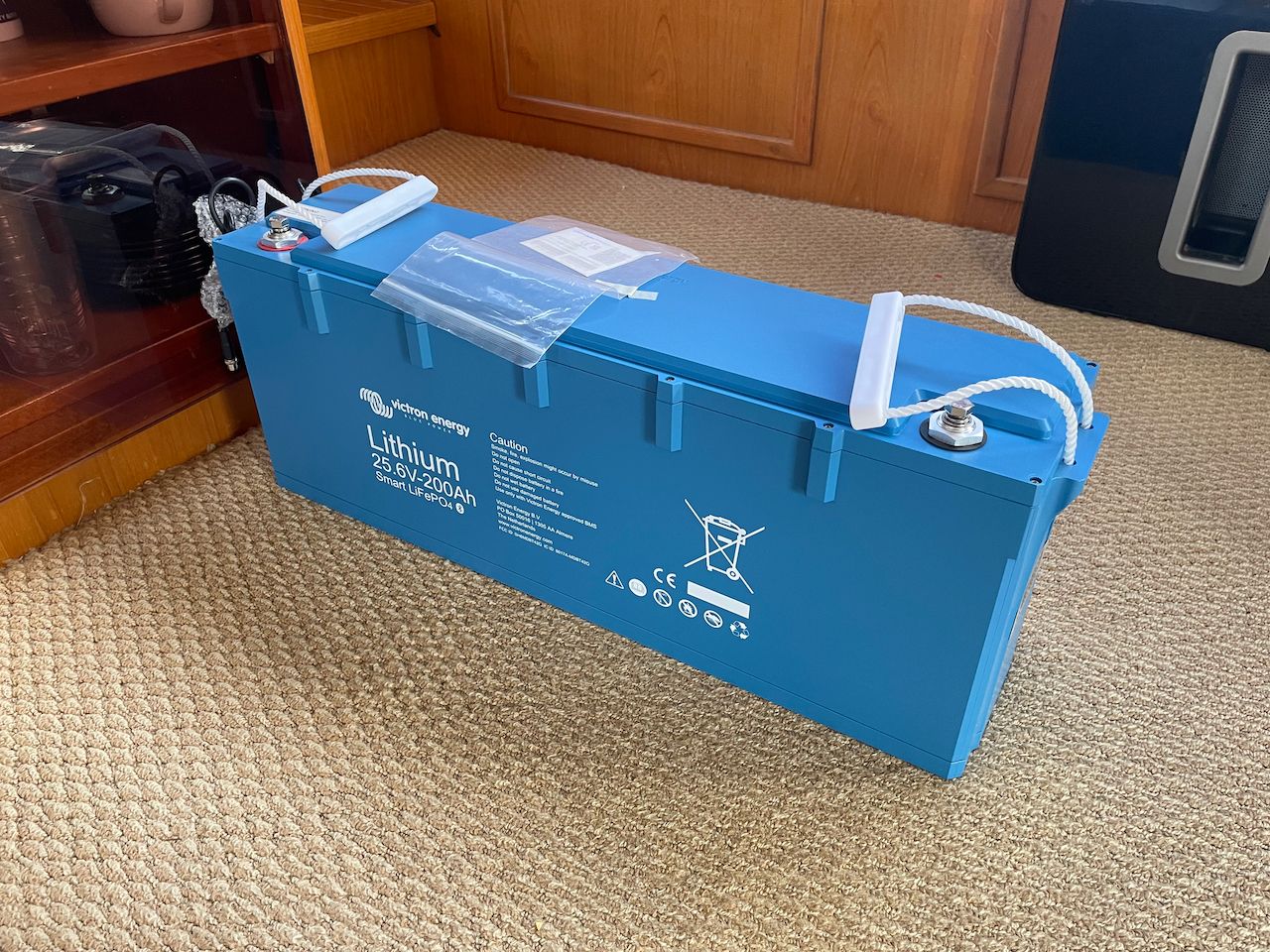
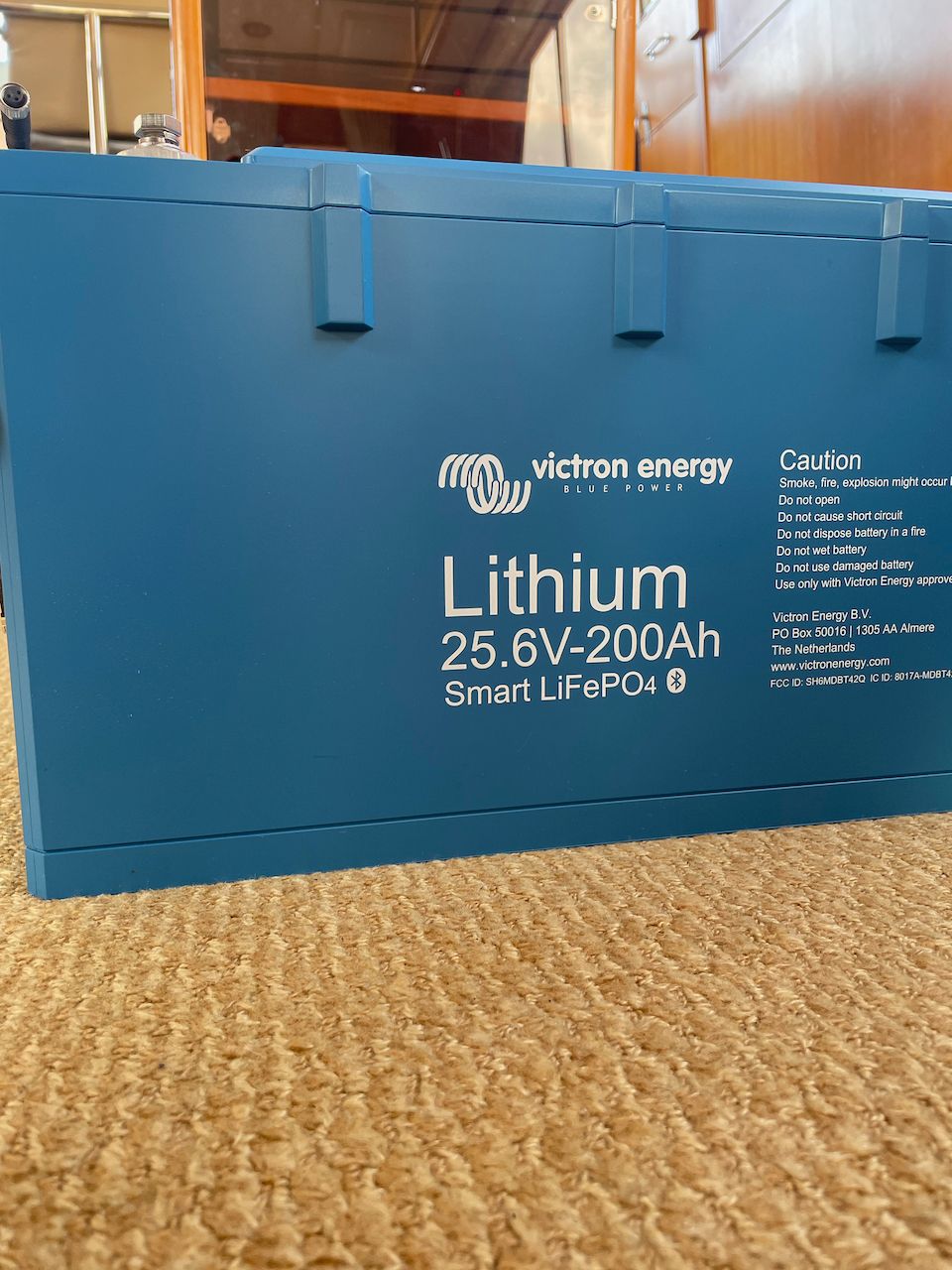
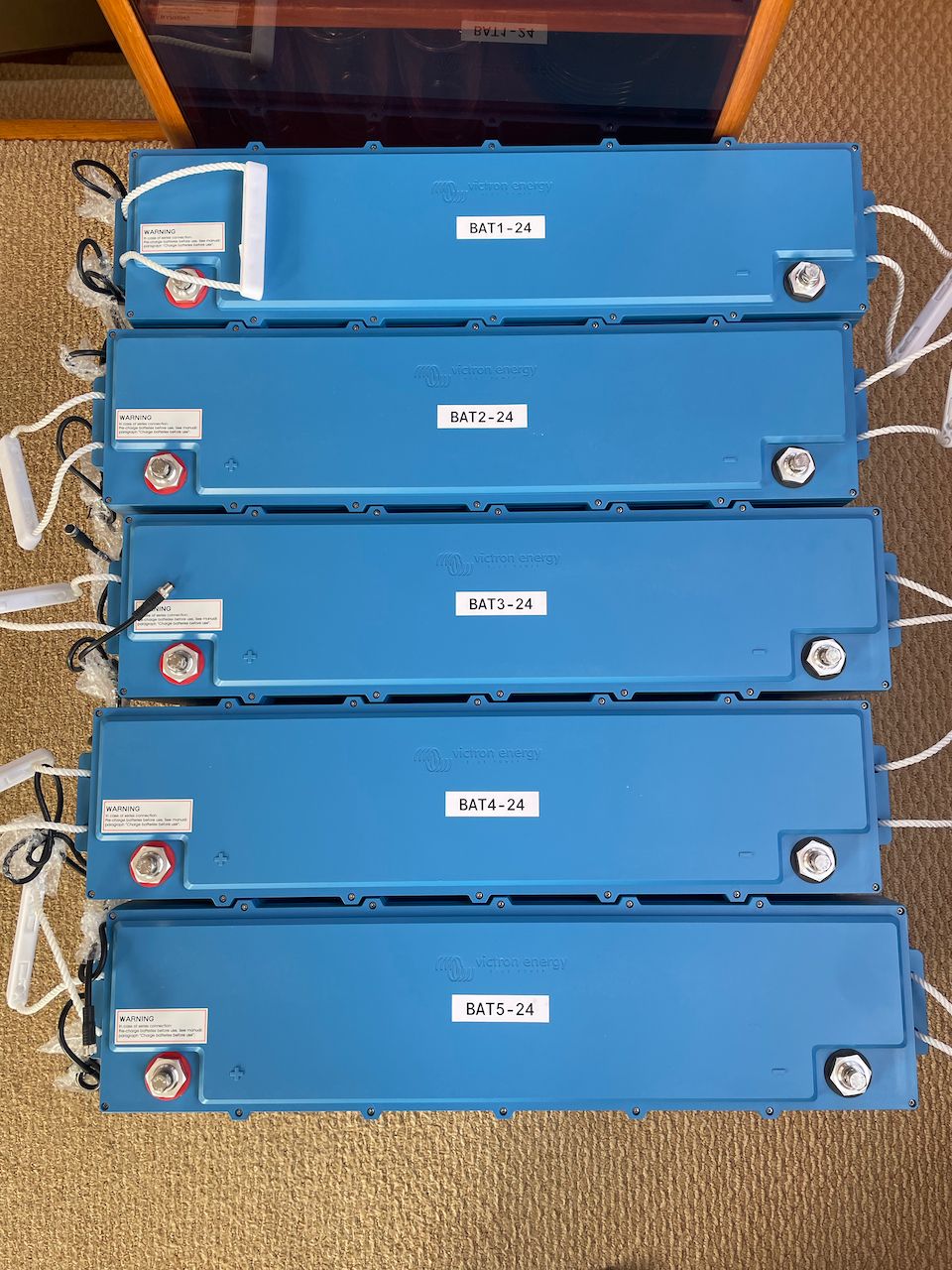
Victron LFP-Smart 25.6/200-a LiFePO4 batteries
They are smaller than the previous version, lighter, and have a more thoughtful form factor (in my opinion). I ended up getting 5x of these for a total of 1000 amp hours at 24 volts. They are well built, have really nice handles, big bolts and connection points, and built in cables to connecto to the BMS.
The existing system was 470 usable amp hours at 12 volts, or 823 usable amp hours if you added in the DC bank, although I never got that out of the system. If you convert the new system to 12 volts, it would be 2000 amp hours which is 1177 more amp hours of capacity. Definitely an upgrade!
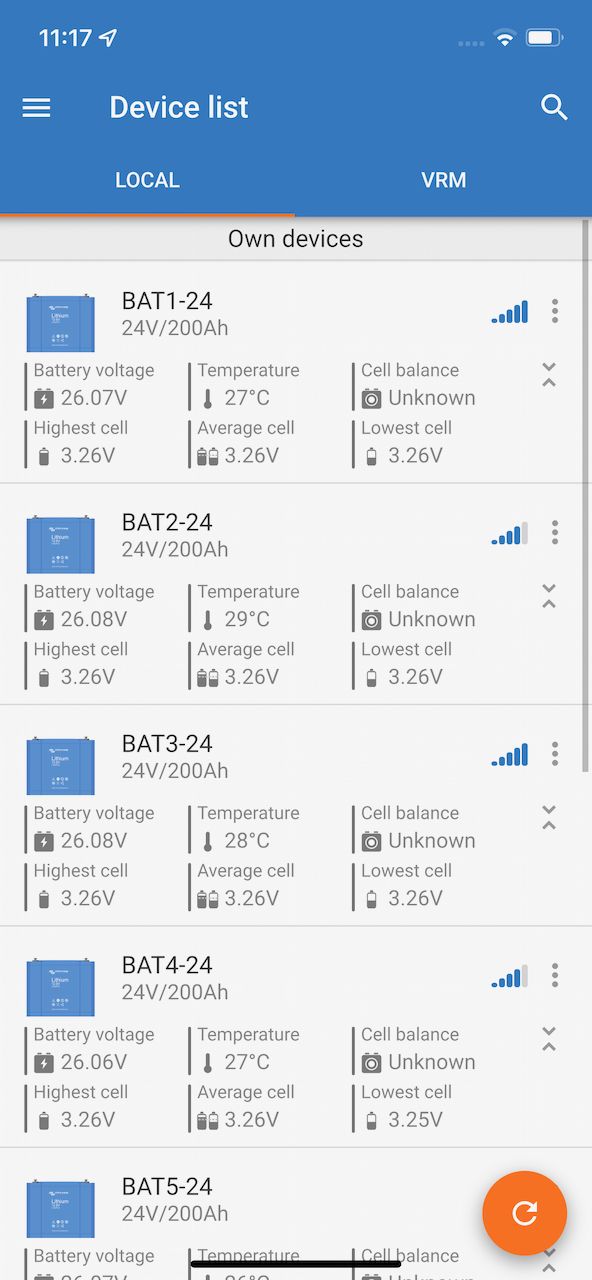
I was able to install the new batteries in the engine room in roughly the same space as the original 6x GC2 batteries, although oriented slightly a different way. That replaces the 6x GC2 house bank and the 8x GC2 batteries in the lazarette that were used by the old inverter.
Inverter / Chargers
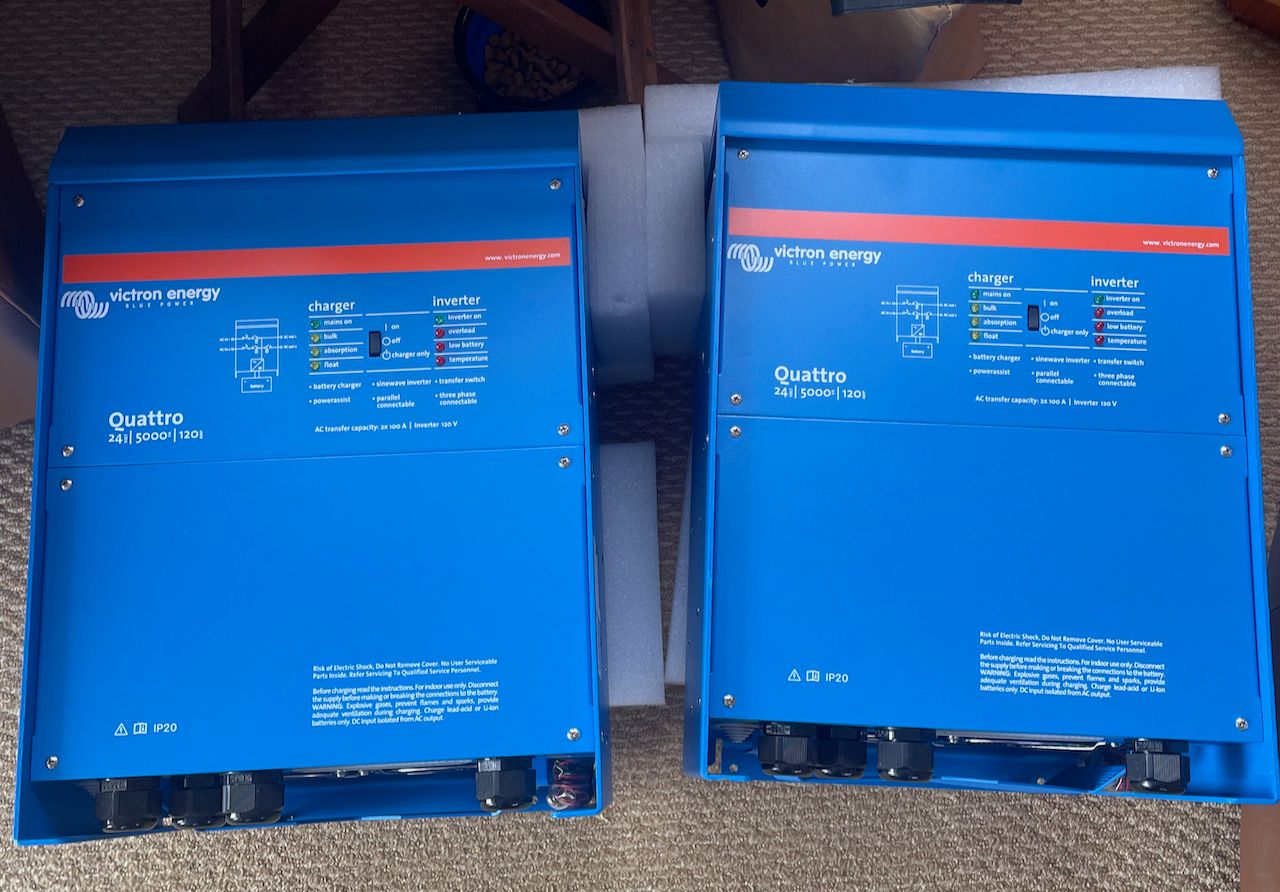
I chose Victron's Quattro inverters for the design because of their general charging and overall capacity, and ability to deal with two AC input sources.
The original inverter was only 3000W, and I knew that I would need a lot more capacity if all AC loads were going to move to inverter. Charging was also a big reason to select these inverters as each one is capable of producing 120 amps of 24v DC. Combining them would provide a maximum of 240 amps of synchronized DC charging to the 1000 amp hour bank.
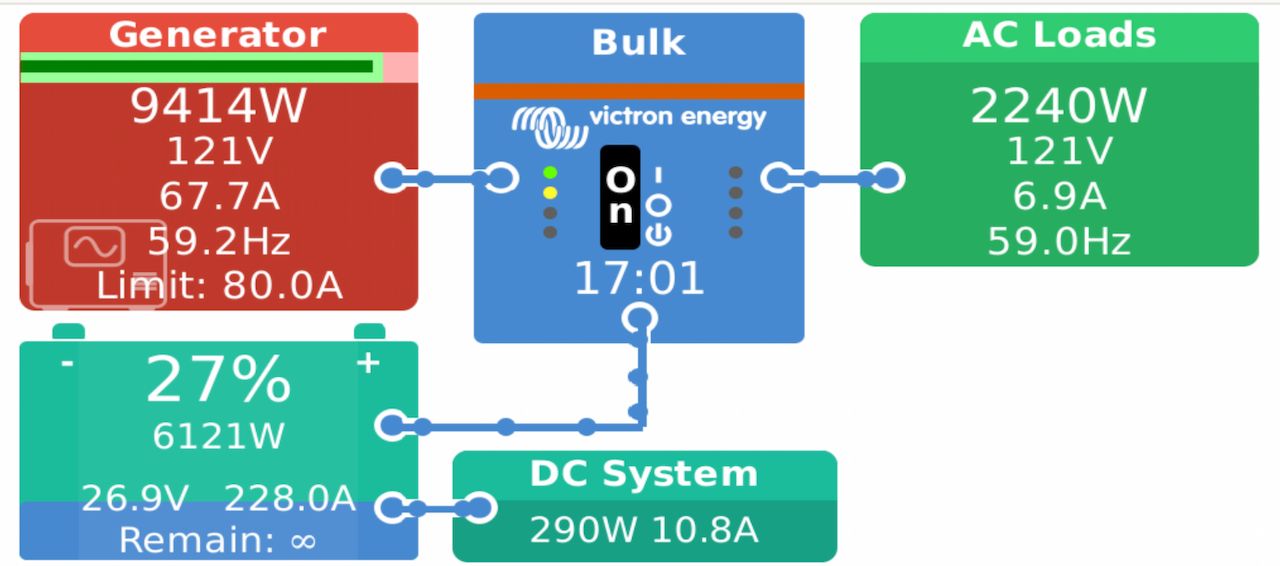
At that charging rate, it would require about 50 amps of AC power. My generator is a 13kW Kohler 120 volt AC model and a maximum of 100 amps of AC. I don't want to run it at more than 80% load or 80 amps of AC, so around 50 amps being dedicated to charging is pretty good. That leaves 20-30 amps of AC power for other loads such as the water maker, and the 5-10 amps of normal AC usage.
Parallel vs Split Phase Inverters
This was one of the biggest experimentation areas for the whole design. The boat came with a 50 amp shore power inlet wired where each phase went to a different part of the panel, but was not wired correctly. Since the boat only has 120 volt AC appliances throughout, and there's no real plan to change that to 240 volt in the short term, I was open to different setups.
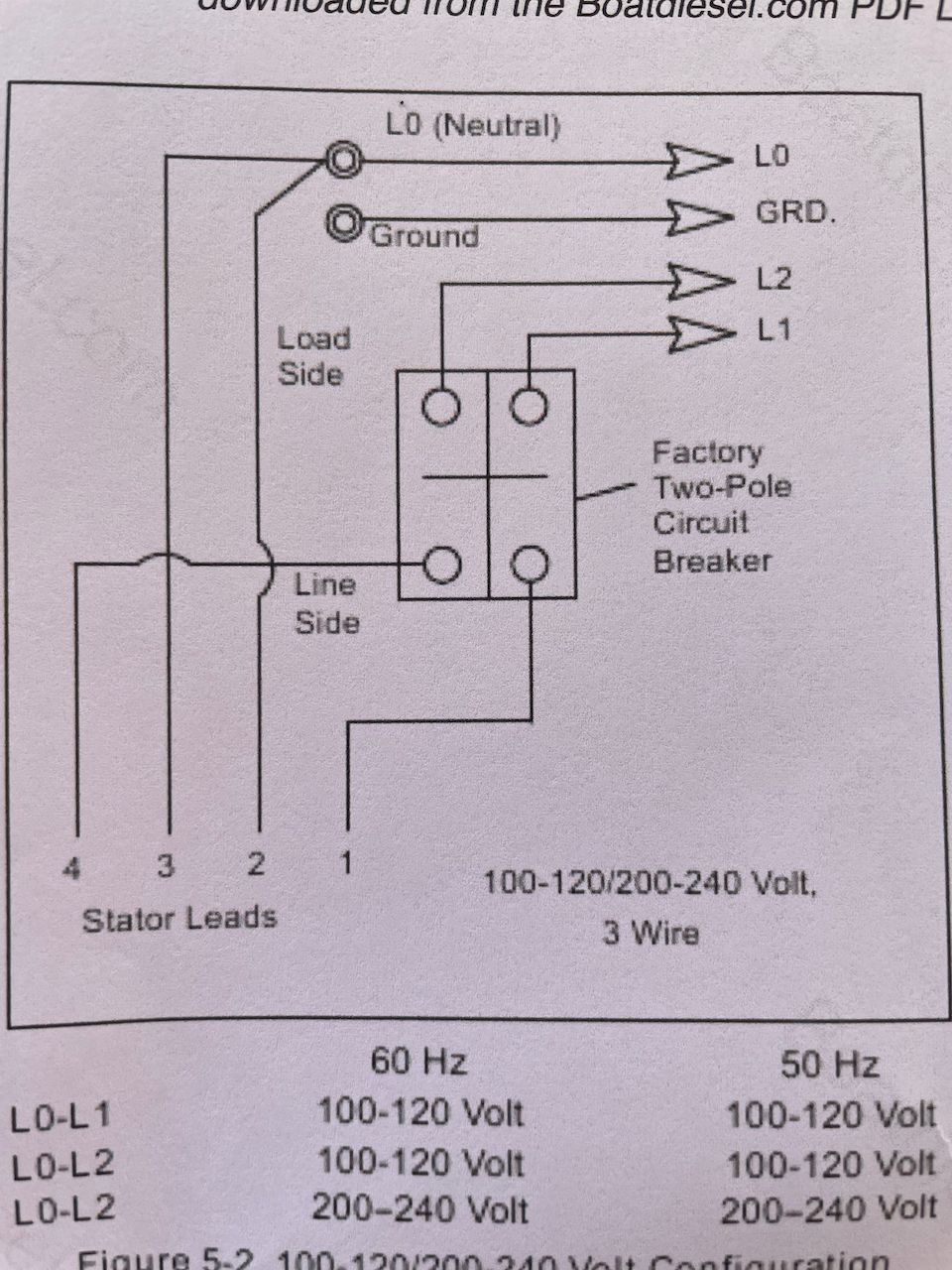
The other wild card was the 13kW Kohler generator. It came wired as a 120 volt AC system, but I had hopes that I could convert it to 240 volt AC given that I knew of two other people with the same unit who had that configuration already. Unfortunately, after a week of experimentation, I was not able to get it to work correctly at 240 volts, and even had a thread on Trawler Forum looking for advice.
I was trying to get both shore power and generator to provide 240 volt AC power with two phases. That would allow me to maintain two separate AC sections on the main panel, each having a phase of power providing 50 amps of 120 volts. This would mean that the inverters would be configured in split phase mode, with each one handling one phase of the incoming power, and capable of outputting both 120 and 240 volts if I wanted.
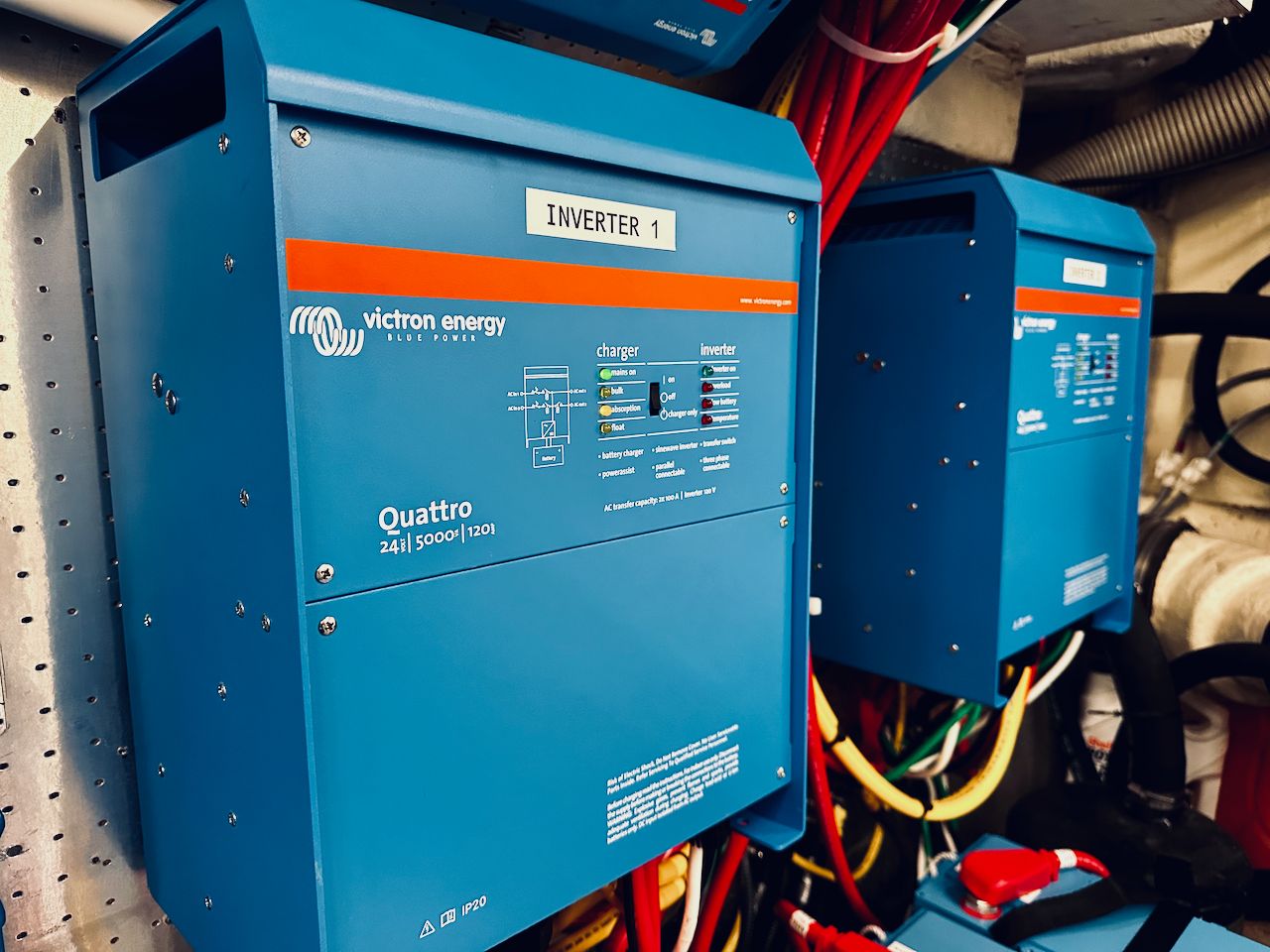
Unfortunately, due to the generator being stuck at 120 volts, I couldn't do that. But it actually worked out better than I could have hoped.
One of my goals was to put as much as possible on inverted power so that there was less messing around turning on/off the generator and circuit breakers when someone needed to run some appliance. In addition, I wanted to make it as simple as possible to run it and not have to worry about balancing phases.
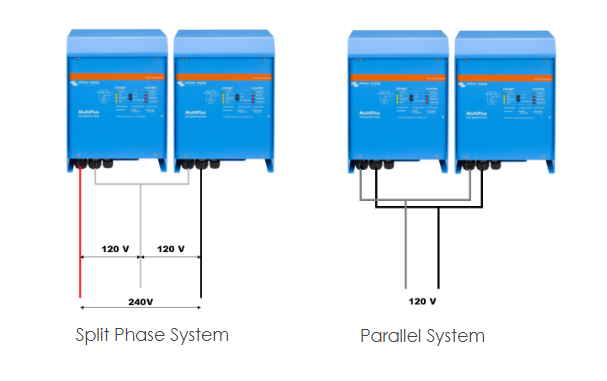
As a result, I configured the inverters to be in parallel which allows for a few benefits:
- Simpler system - less complexity than having multiple phases, breakers, etc.
- Single AC output to the panel - less work to balance phases, all inverter power is available to the entire panel and not split
There is one downside, and that has to do with utilizing the maximum amount of shore power. Originally with 50 amp 240v coming into the boat, I had the ability to split the various AC loads across two phases - essentially two banks of 120 volts each at 50 amps. With this new configuration, I will only be using one phase of the two, which means I can only get 50 amps total out of shore power.
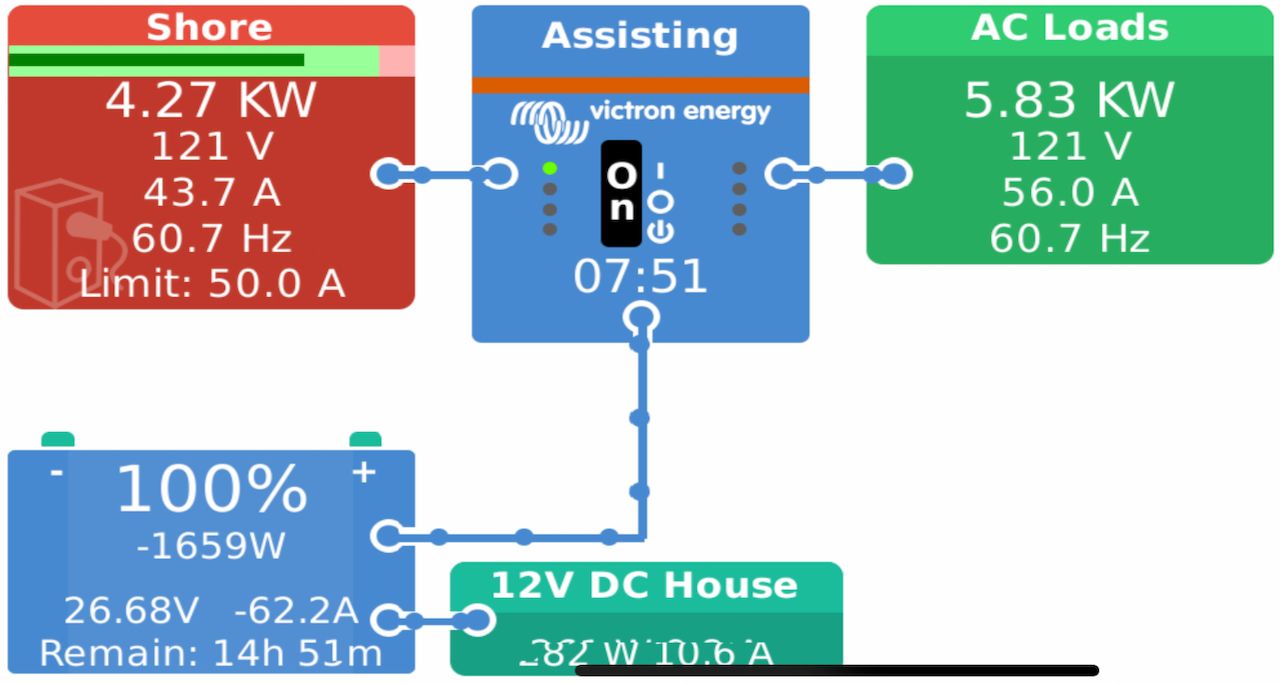
I was initially worried with this limitation, as I would like to have as much power available as possible. However, after 6 months of using the setup, I have no regrets and have had zero issues. Victron's Power Assist feature has stepped in wherever I've needed more than 50 amps of power, which has been rare. During normal use, I rarely ever need a full 50 amps of power continuously,
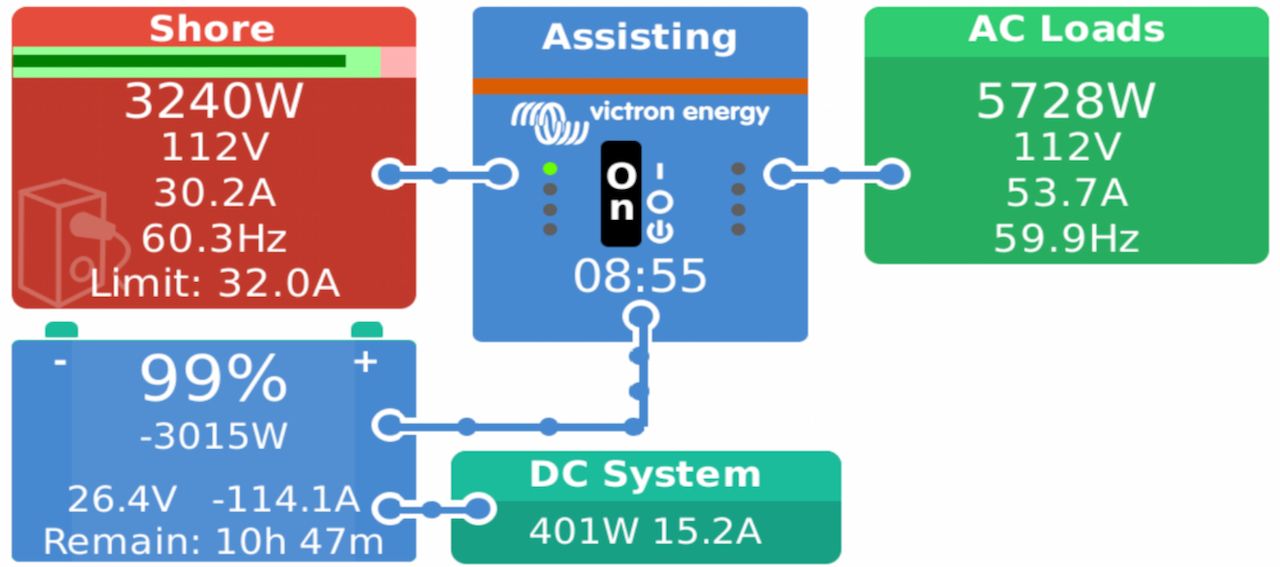
I've even used the system with 30 amps of shore power in a couple of places. It's worked just as you would expect, providing more power - here around 54 amps - while needed, and then charging the batteries back up later.
Everything on Inverter
As a result of this setup, I chose to put everything on the inverter which has been wonderful from a usability perspective. We can run anything and everything all of the time, regardless of whether we have shore power or generator power.
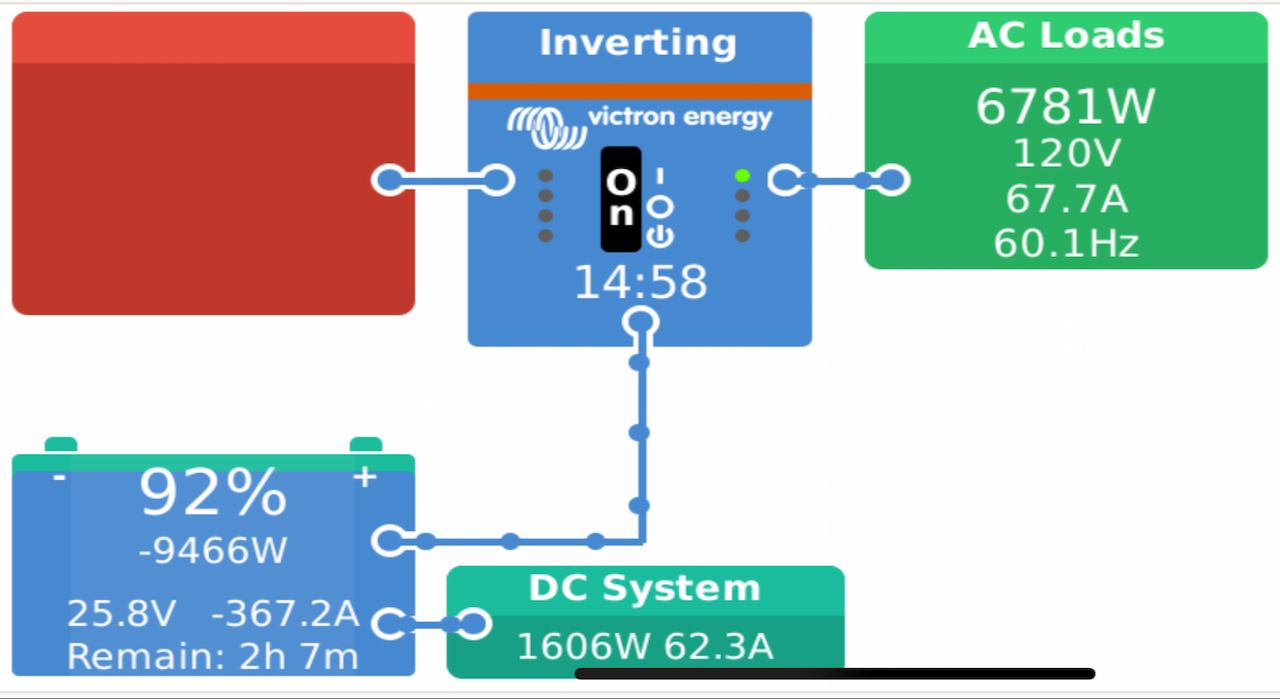
That makes a big difference for folks who don't know how a boat works - they don't need to ask to use something - everything just works. The downside is that it does require a bit more thought around what you leave on all of the time. I have big block heaters for my engines which I've left on once or twice, only to notice them a few hours later. I'll take the inconvenience for the overall simplicity of the entire system.
Wiring
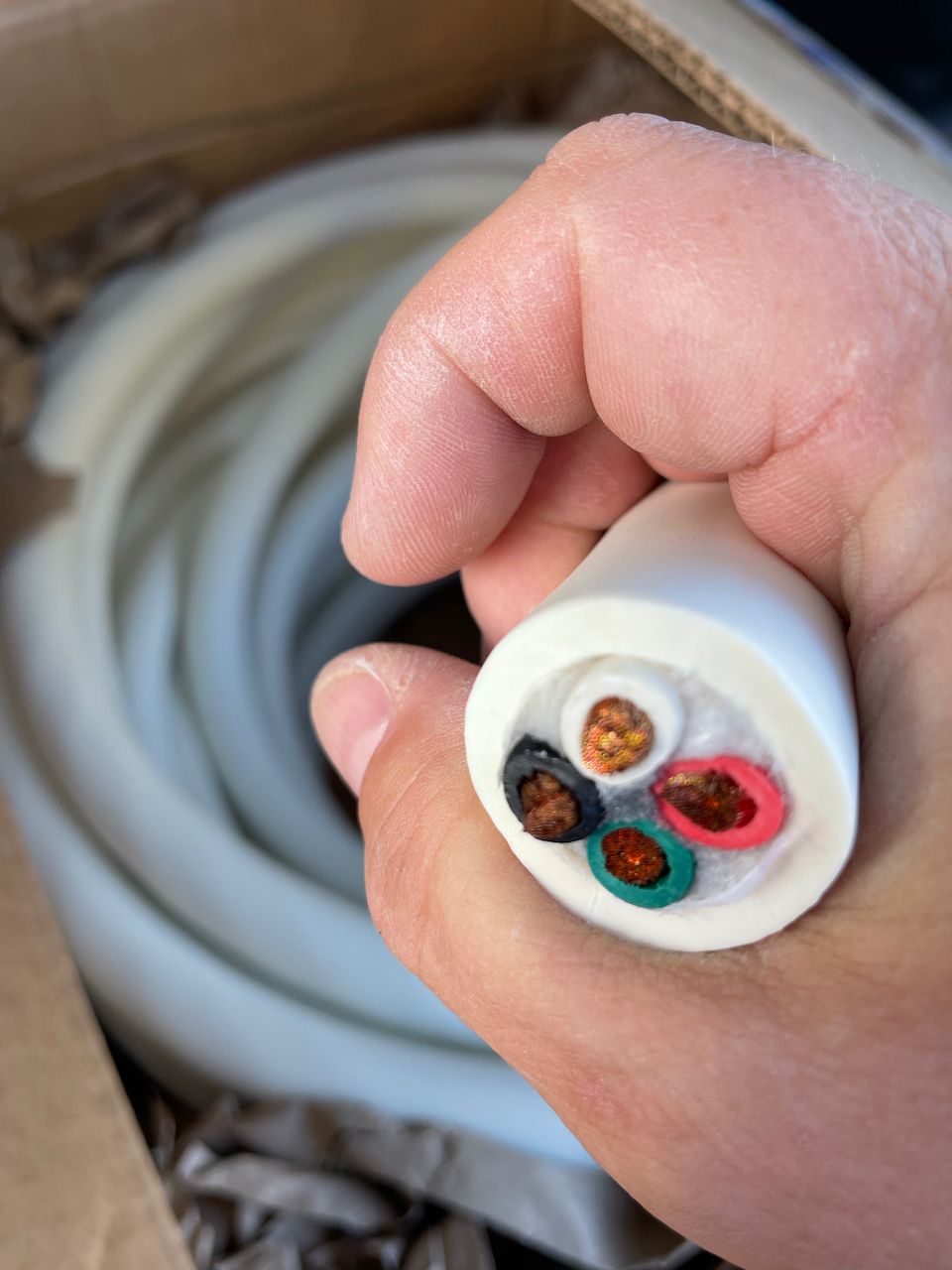
With the new design, I had some wiring challenges with the AC power side of things. First, the shore power inlet is amidships at the pilot house door on the starboard side. The AC panel is right there as well, but I wanted all of the AC power to go through the inverters to take advantage of Power Assist and all of the other monitoring capabilities. This meant that I needed a new cable from the shore power inlet to where the inverters were being installed in the engine room.
I also needed a new set of wires from the inverters back up to the AC panel, as the previous inverter was only powering a small part of the AC panel, and I was moving everything over to run through the inverters. I chose some beefy 6 AWG wires with four conductors in them. I had to run it from the pilot house down the side of the boat and into the engine room. Thankfully Kaos has a cable tray the whole way, and it was pretty easy! That's a rarity based on previous boats and customer installs.
12 Volt DC System
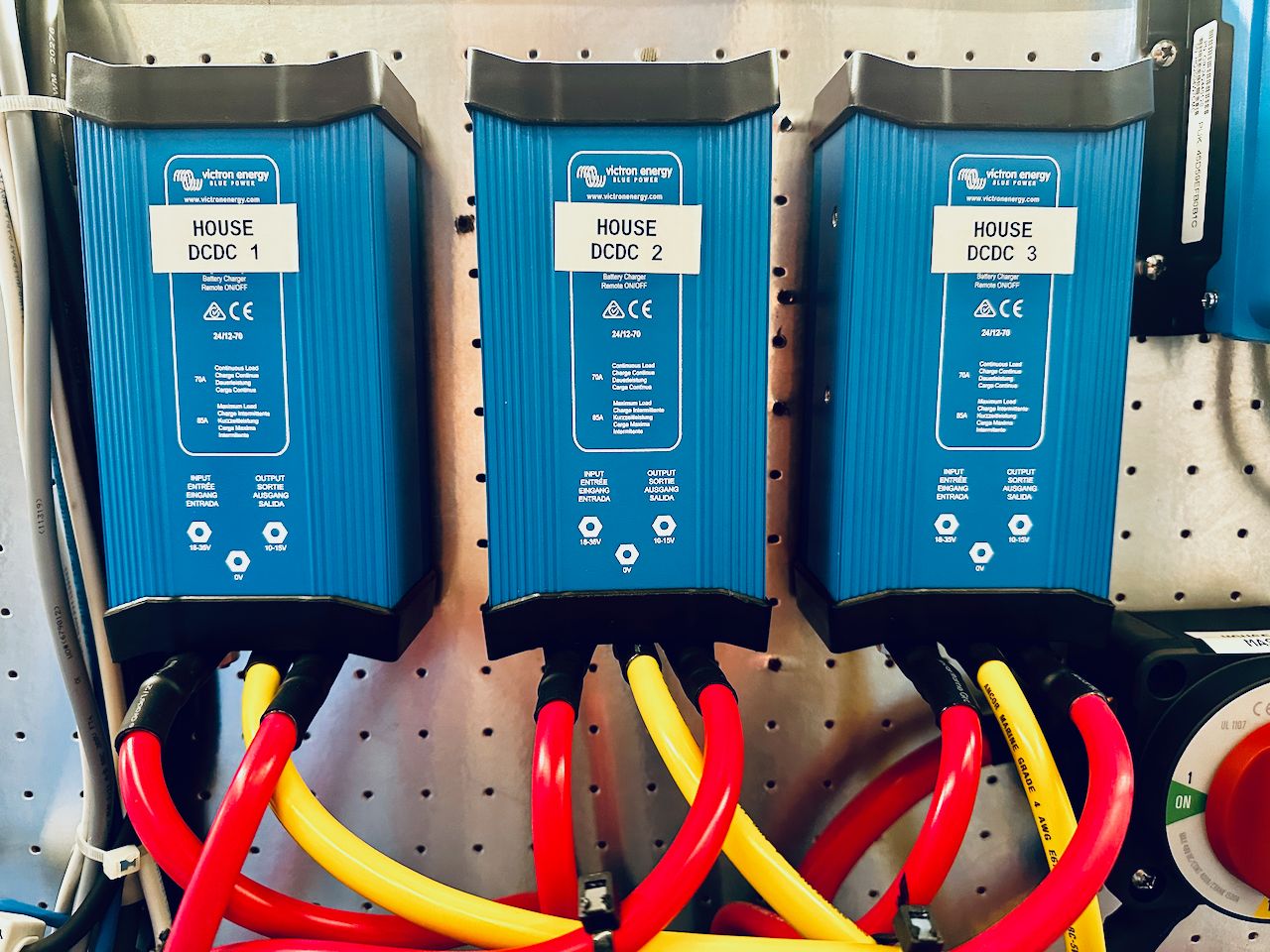
The entire DC system on Kaos is 12 volts, and I was not replacing or upgrading that as part of this project. I tried a number of different combinations of things over a 2 month period, and ended up settling on 3x Victron Orion DC-DC power supplies that convert 24 volts to 12 volts, and are each capable of 70 amps. That gives me a total of 210 amps of 12 volt power, which is more than double what I calculated my max usage was. It also provides some redundancy since I have 3 units in case of a failure.
These little boxes actually worked better than a dedicated AGM battery bank that had similar amperage numbers. While the batteries could last on their own without anything else powering them for a while, the voltage drop was significant with any sort of decent load. The Orion power supplies don't sag quite as much, and I was able to dial them up to 13 volts and get a consistent voltage out of them compared to a battery.
The one challenge is the 12 volt anchor windlass where in some situations, it draws an enormous amount when it is heavily loaded and causes a voltage sag. This causes some sensitive things to restart. The eventual plan is to upgrade the anchor windlass motor to 24 volt and connect it to the existing 24 volt thruster bank.
Lynx Distribution, Shunt and BMS
I had used the Lynx distribution system on a few other customer projects, but never on my own boat. I had also never used the BMS or Shunt products from the Lynx series.
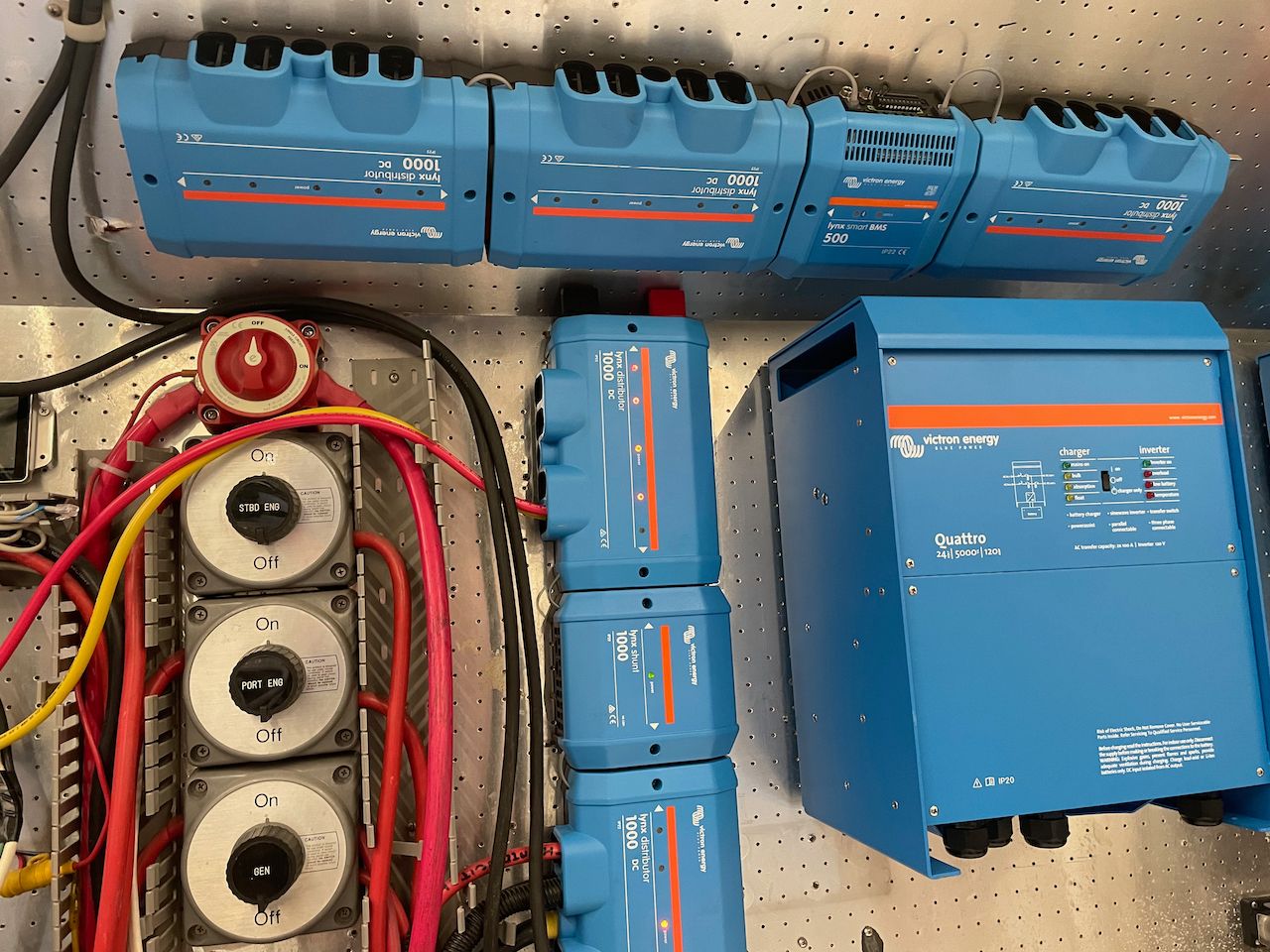
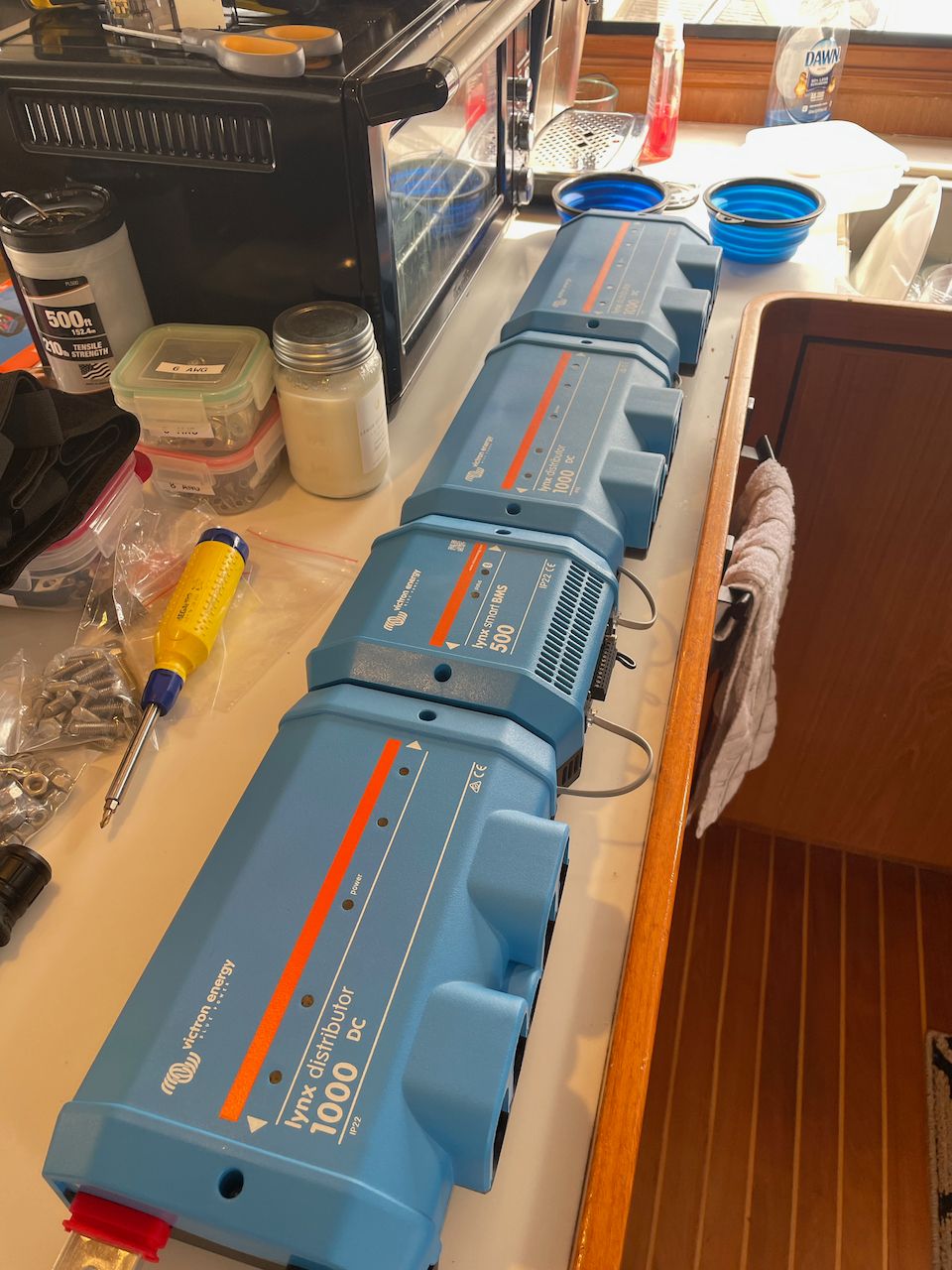
Lynx distributor and BMS
I chose the Lynx distributor for the battery and inverter connections. Each is fused and connected to the rest of the system so that any blown fuse causes an alert, and provides details on which fuse has an issue. I looked at BlueSeas and Marinco Pro Installer bus systems, but they would have ended up being bigger footprint-wise, and some of them had lower amperage ratings that didn't meet my design.
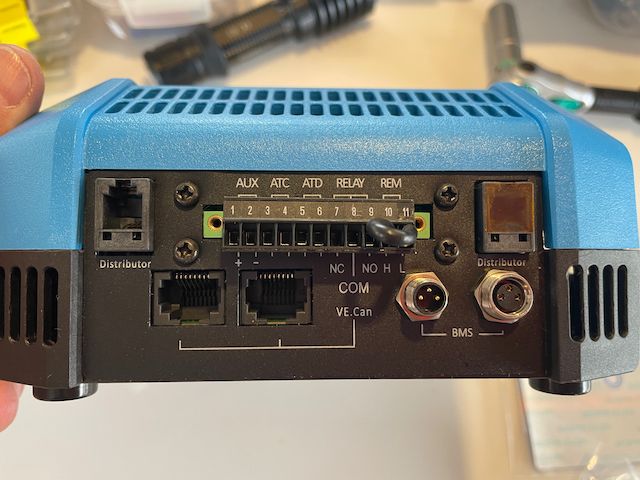
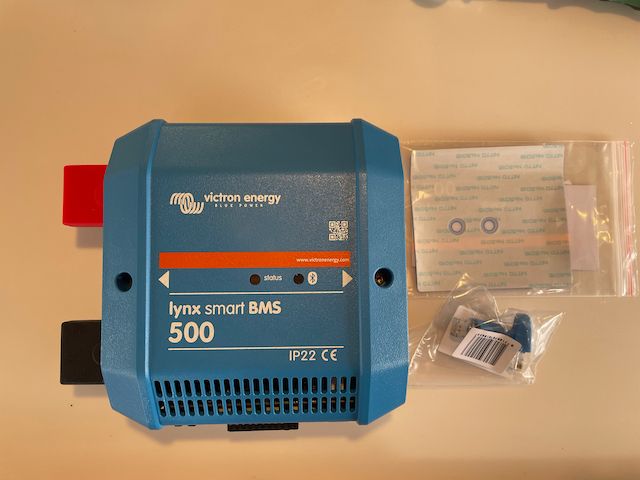
Lynx Smart BMS
I chose the Lynx Smart BMS after a lot of painstaking research. This is one of the challenges with Victron - they have too many choices for shunts and BMS's, and each of them have some big gaps that cause design issues or changes. The Lynx Smart BMS is probably their most advanced, and provides a lot of nice features. It has a dedicated connection for the distributors to read the fuse statuses, for the batteries to manage them, VE.Can to connect to the inverters and GX device, and individual connections to power the GX system.
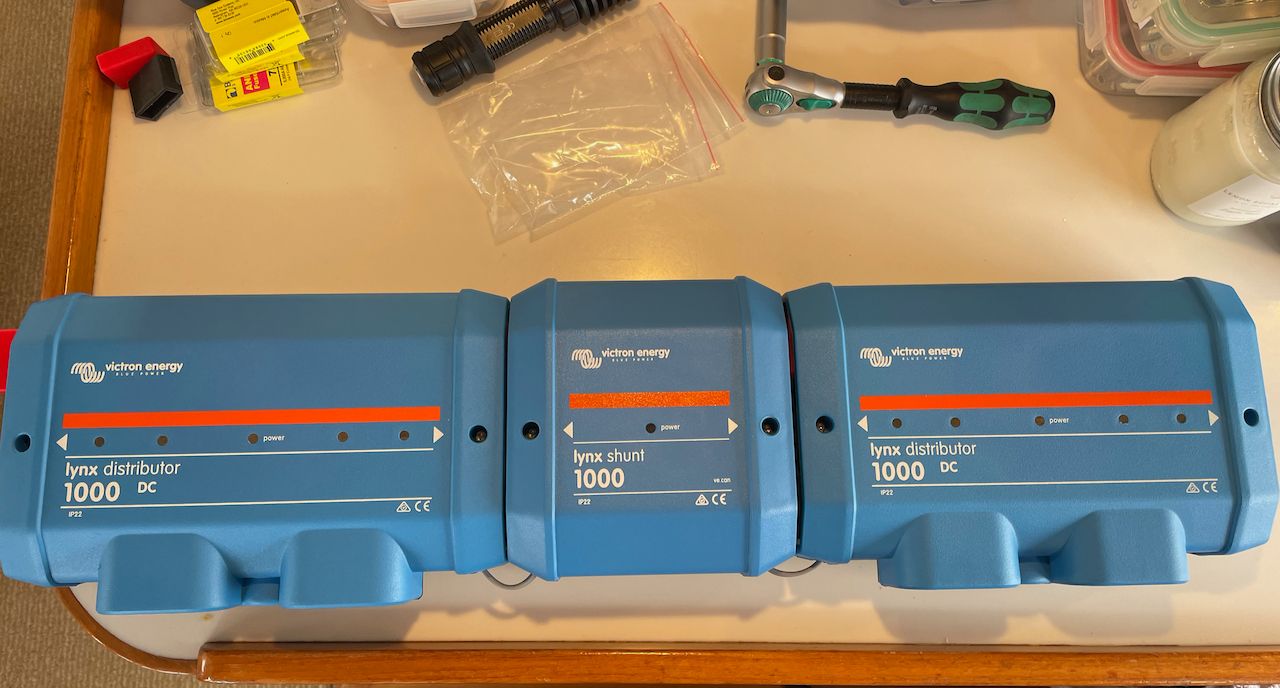
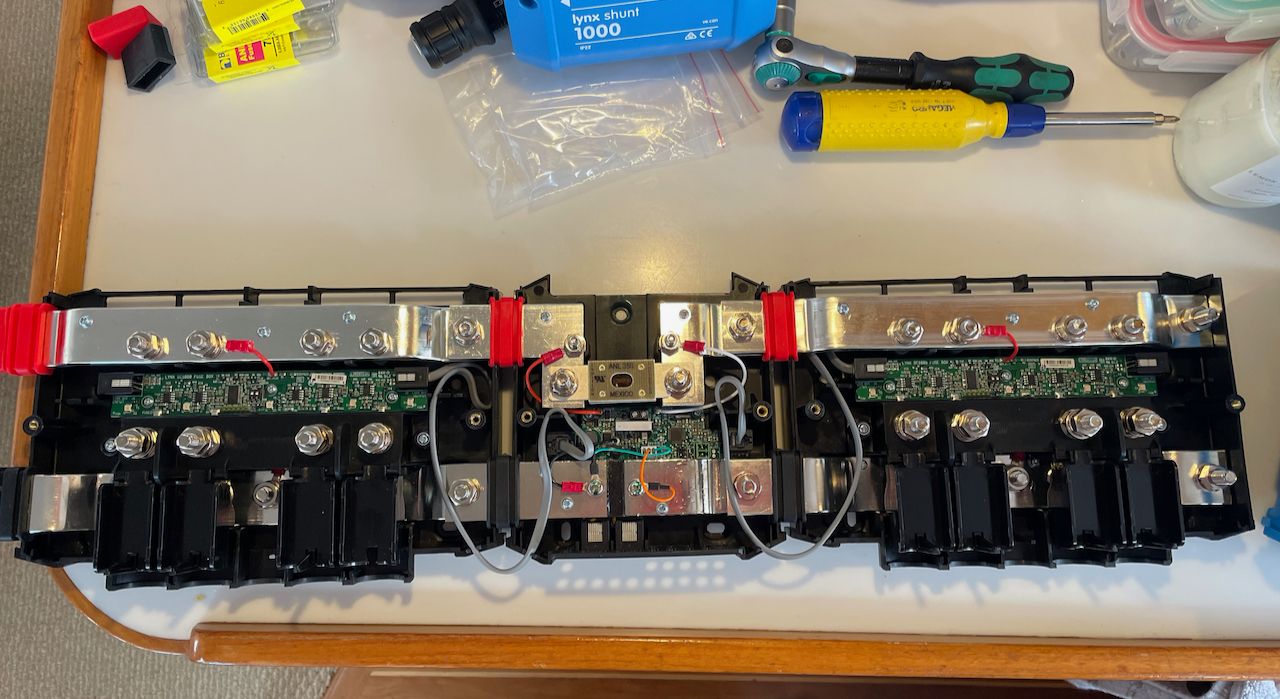
Lynx distributor and shunt for the 12 volt system
I also chose to use the Lynx distributor system and shunt for the existing 12 volt system. I used one side of the distributor for the three Orion DC-DC power supplies that run the 12 volt system and their input power. Three fuses on that side protect the power supplies.
The shunt is there so I can monitor the amount of power that the 12 volt system is using, although you can sort of already see that with the "DC System" statistic on the GX display. On the other distributor I have 2x 0/2 AWG cables going to the main DC panel in the pilot house, one going to the diesel heater, and one going to always on circuits in the engine room.
There are a lot of other features, and issues, with the Lynx Smart BMS, shunt, and distributors that could benefit from a dedicated article in the future. Even so, I have been very pleased with the clean install of the Lynx system, the shunt, BMS, and other protection pieces all built in, and how well it has worked so far.
Charging other battery banks
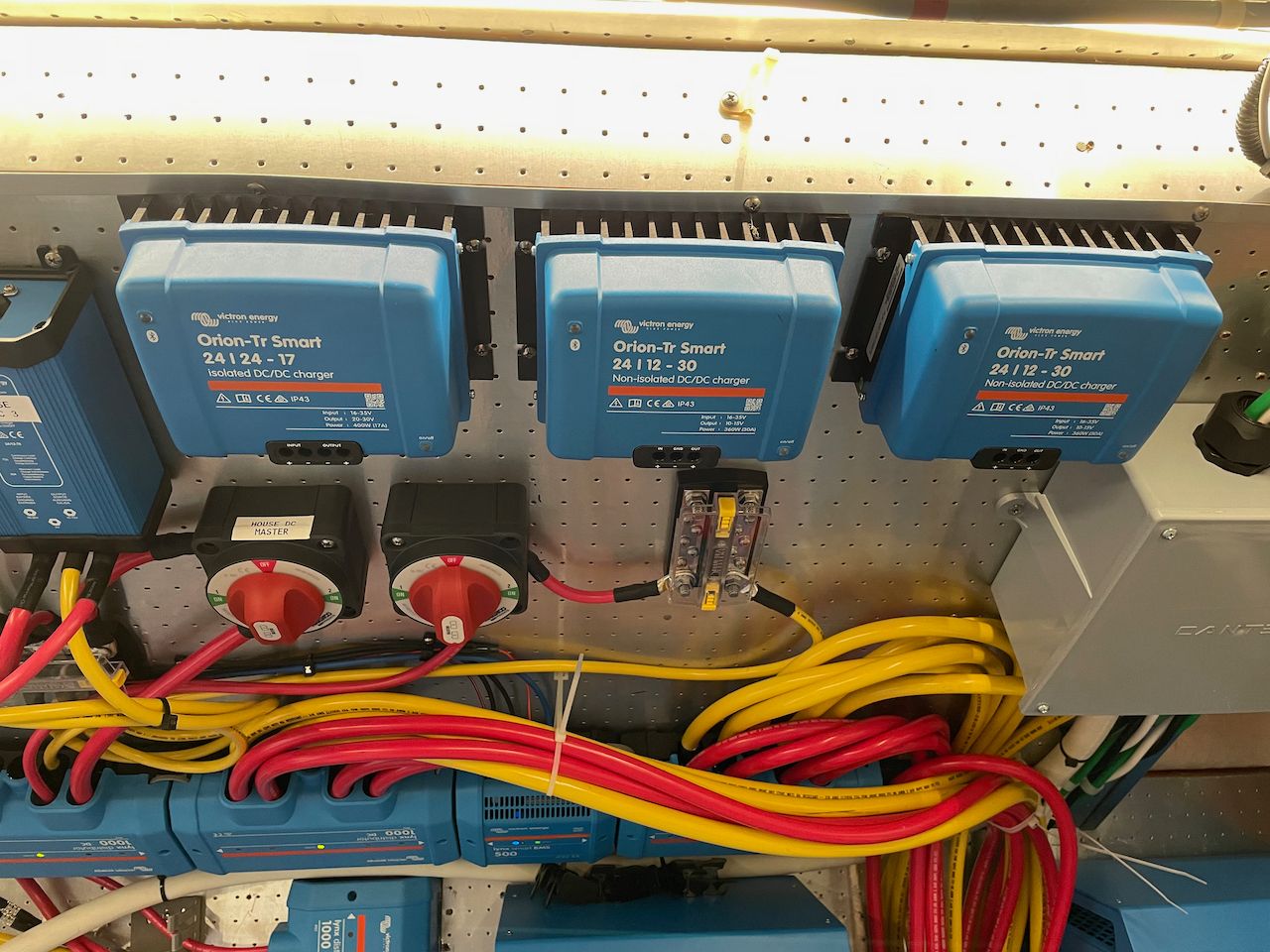
Just like Grace and Rendezvous, I chose to make charging other banks as reliable and simple as possible. I hate ACRs or other combiners because of what can go wrong with charging the wrong thing or the current flowing the wrong direction. They also do not work well with different battery charging profiles or chemistries, which I definitely have in this system:
- Main engine start battery bank - 4x group 31 "maintenance free sealed" flooded batteries.
- Thruster battery bank - 2x group 31 "maintenance free sealed" flooded batteries
- Generator start battery - 4D flooded battery
All of these batteries will be replaced in late 2022/early 2023 with group 31 AGM batteries from Lifeline, but weren't part of this budget / project.
I chose various versions of the Orion-Tr Smart DC/DC chargers - one for each bank - which are supplied from the main 24 volt inverter bank. This guarantees that all three of those battery banks are always charged with the proper profile, that current only flows one way, and I can monitor them via the VictronConnect app. This is similar to what I did on Rendezvous, and provided a very reliable, hands off way to ensure other battery banks are always charged.
Alternator
Unlike the last two boats, I chose not to install high amperage alternators for a few reasons. First, I had lots of challenges with regulators and alternators being reliable all of the time with high outputs. It required a lot of attention and time, and although they did provide great charging underway, my setup with the dual Quattro inverter/chargers provided a much more efficient and predictable way of charging. Second, the Caterpillar 3208 engines in Kaos had limited space for alternators, although one was modified for a larger one. I didn't really want to mess around with additional modifications.
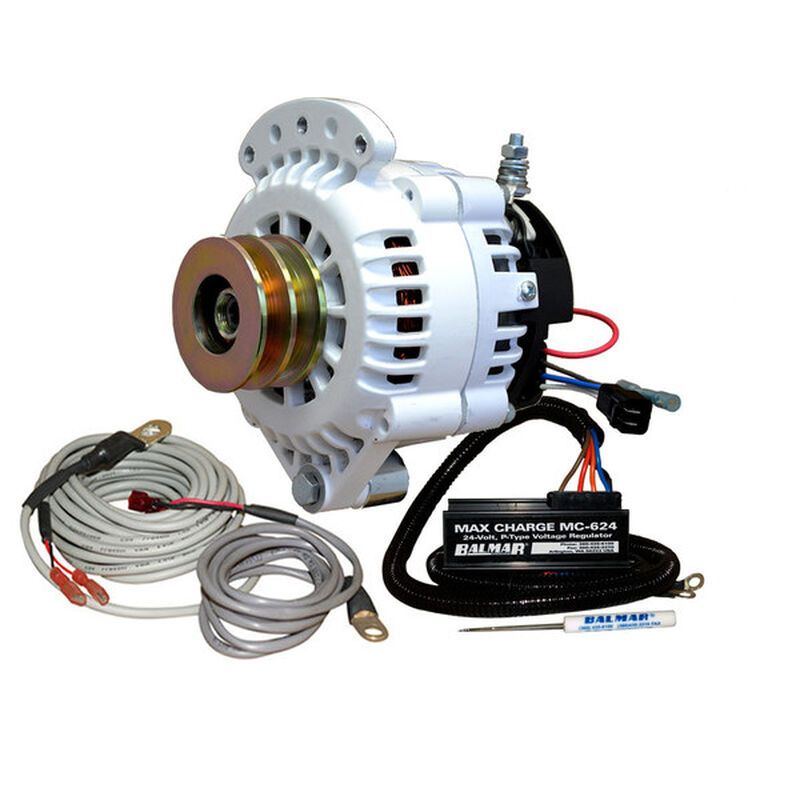
You may also notice that I am using a Balmar regulator and alternator instead of the Wakespeed systems I've used in the past. I did start with a Wakespeed WS-500 regulator in this system, and it was connected to the Lynx Smart BMS. Unfortunately, it did not end up working reliably, and I removed it. I ended up with a 45 amp 24 volt alternator paired with a Balmar MC-624 regulator and a Balmar alternator protection device.
This means I don't have a huge amount of underway charging, but it is enough that I don't end up discharging while underway, and have a small amount of amps going into the battery bank. There is also a plan to add a second 24 volt alternator to the other main engine - right now it is a 12 volt stock alternator that is disabled. At that point, I would have ~50 amps of charging underway, which is great to have.
The biggest reason for my change here over previous boats is the complexity and issues that I had with regulators and the expense of the higher output alternators. I'm hopeful that in the next few years these will become more usable for every day folks.
Using the System
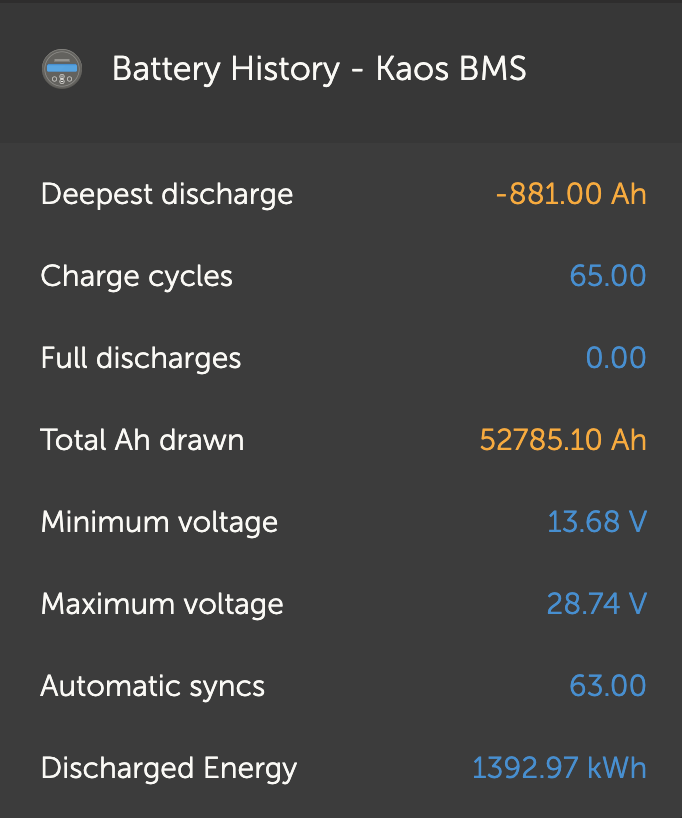
So far I have been extremely pleased with the system. Since installation, it has run flawlessly without any issues for 6 months in all sorts of conditions. During this time, I was at anchor 70 days and ran the generator about 65 of those days. Almost every time I ran the generator, I ended up running many other systems including the water maker and laundry, putting more load on the inverters. Almost always, the generator is at 70-80% load during the entire run time, exactly as I had planned.
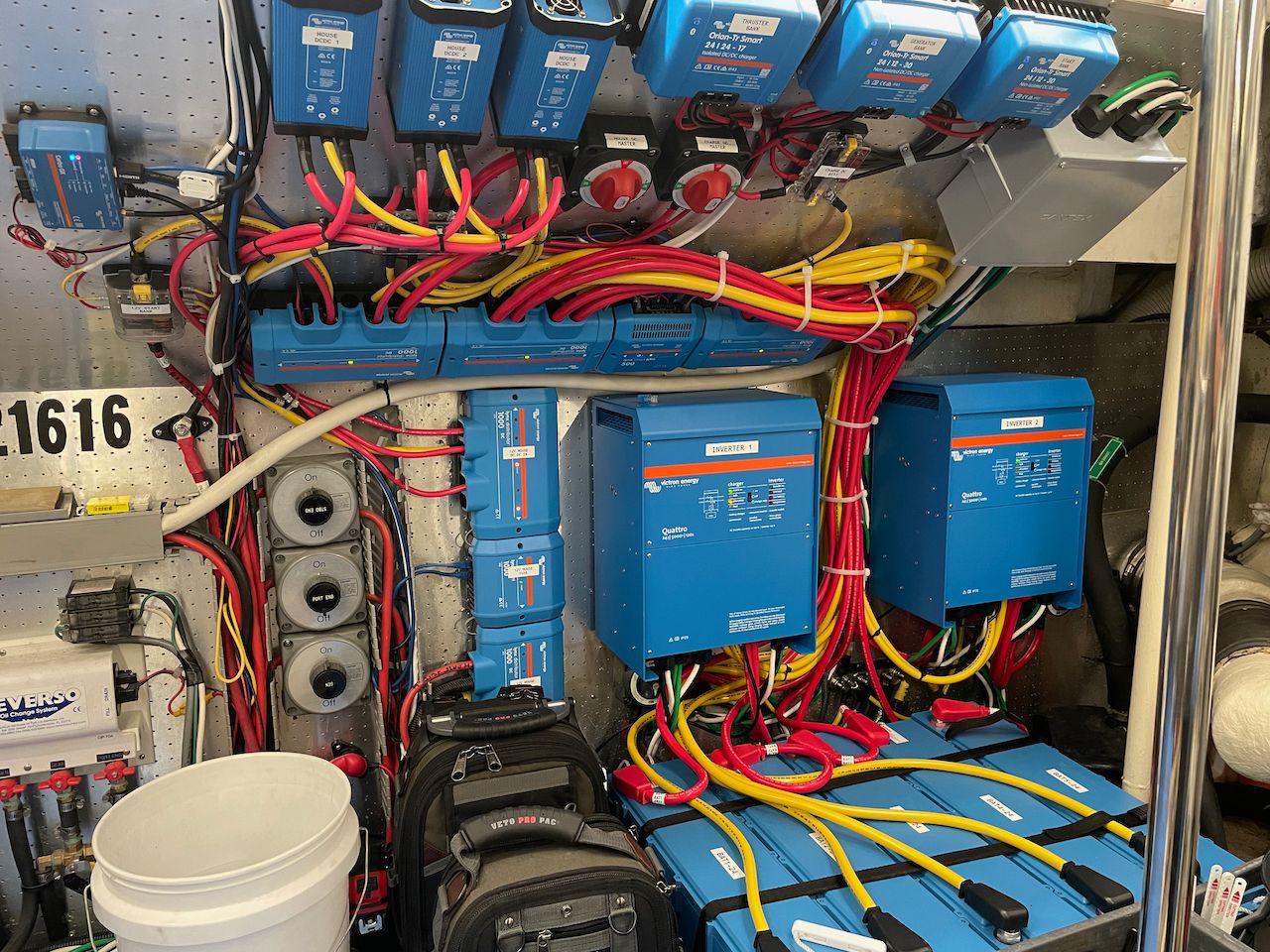
The capacity is enough to run the whole boat for 2 days without charging, and probably longer if we weren't so lazy. As with any other boat I've had LiFePO4 on, you tend to not be as crazy with managing lights and electrical usage, which I'm OK with. If a system makes my time on the boat less stressful, that's a win in my book.
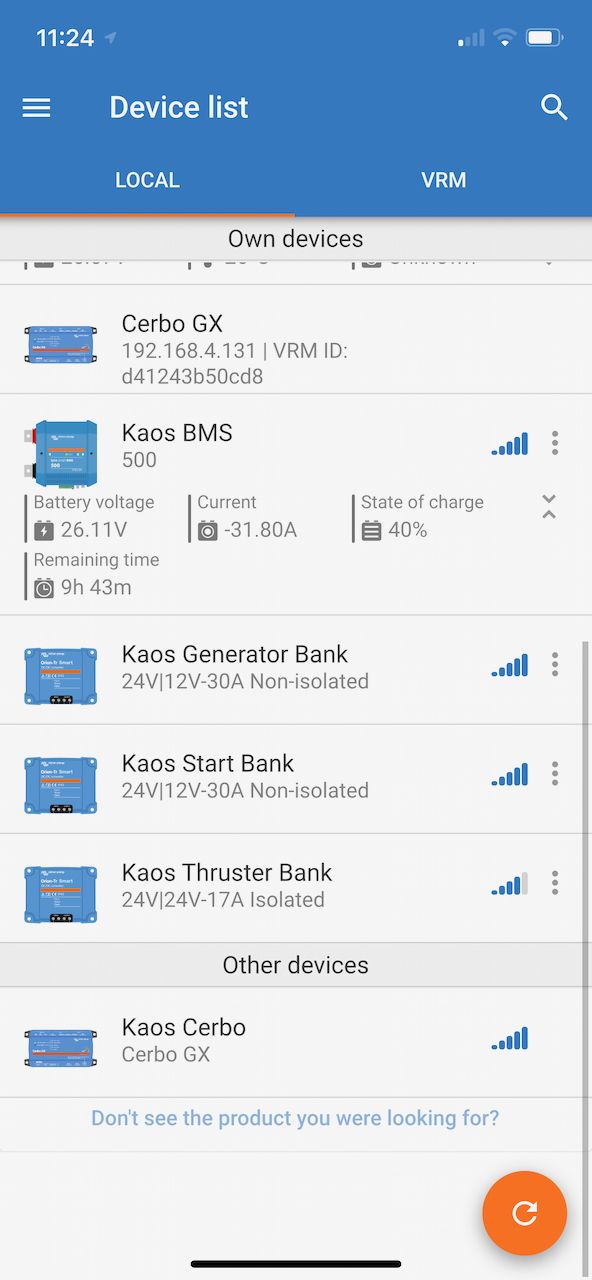
Visibility and control has been great. The other battery banks have been charged well, and the changes to cabling, fusing, and connectivity have not caused any issues. I've noticed a more stable power system in general, especially on the 12 volt side since it is being supplied by fixed power supplies at 13 volts.
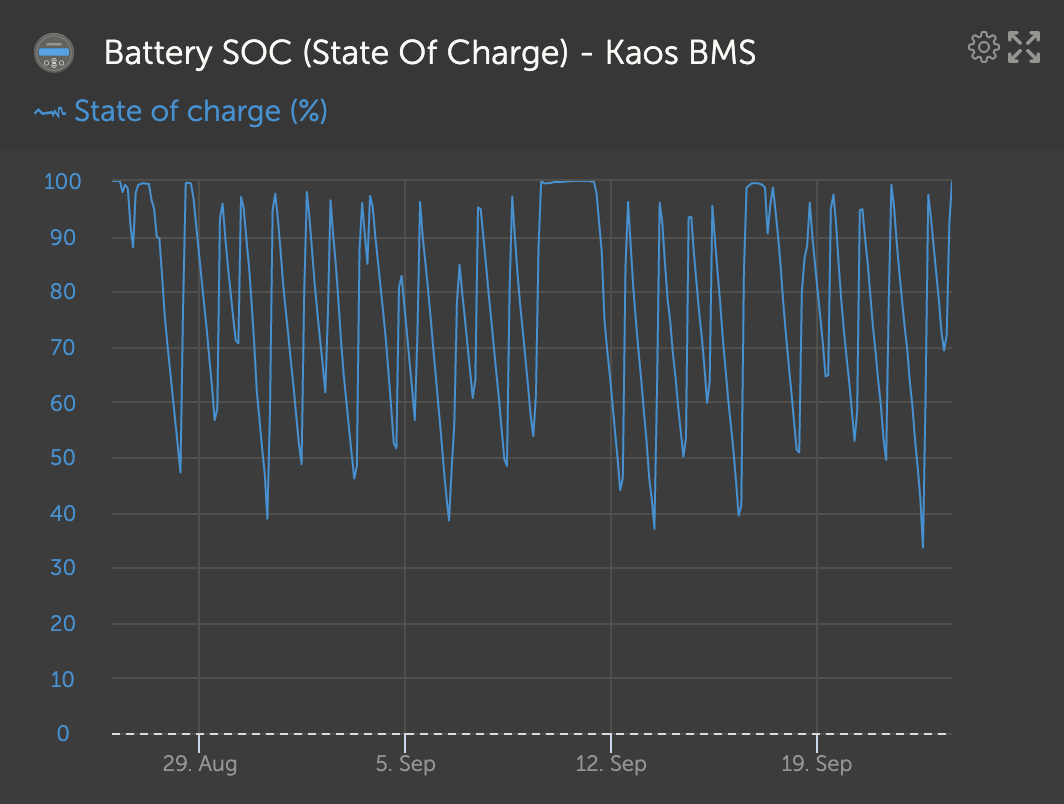
Average generator run time per day is 1-2 hours, depending on state of charge and also how much water I need to make with the watermaker. Since everything is on inverter, it also means we can use the boat systems whenever we want, and choose when to run the generator if it is more appropriate. That takes a lot of stress off of the captain having to plan when to run things, and worrying about making noise late in the evenings. We even ran our air conditioning while at anchor a number of days this year just on battery power with the smoke and hot temperatures. I'm very happy with the reliability, visibility, and capacity of the system.
Challenges
12v windlass - this is connected to the 12 volt house system which gets power from the 3x Victron Orion 70A DC-DC power supplies. During normal use, there aren't any issues, but if the motor is put under higher loads, there is a voltage sag. That results in voltage sensitive things restarting or power cycling, which I want to avoid. Eventually, I will be replacing the windlass motor, or I might upgrade the whole windlass to a slightly larger size, and switch to 24 volts. This will then run back to the existing 24 volt thruster bank and get it off of the 12 volt DC-DC bank, which will eliminate this issue.
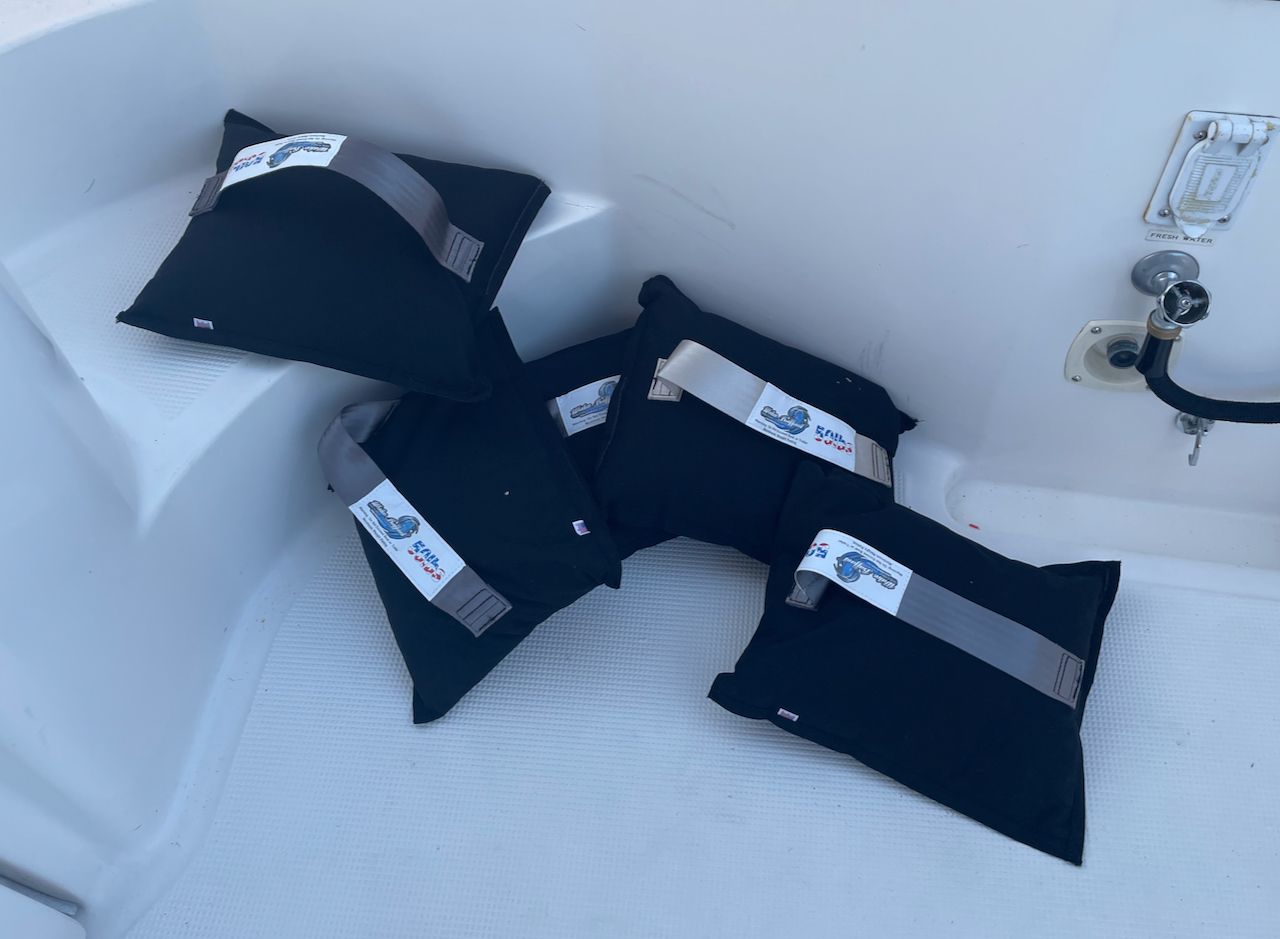
Listing - removing 10x GC2 batteries from the starboard lazarette was great in terms of removing weight, but it created a list. I completely reorganized the storage in the lazarette, but there was still a list. I ended up purchasing a number of 50 pound ballast bags from Wakeballast and placed them in the starboard side to correct the list.
Orion data - there's no way to get any data out of any of the Orion DC-DC power supplies for my 12 volt system, and you can only get data out of the Orion-Tr DC/DC chargers via Bluetooth and a phone app. It would be great if Victron added at least some basic data that you could plumb into the GX platform.
Lynx limits - there are limits around the Lynx distributors (max of 4, and I have 5), Lynx Smart BMS, and Lynx Shunt that are all weird things to work around from the data gathering perspective. None of the issues cause system problems, but for the cost and complexity, you would think they would have thought about these issues. Some are supposed to be addressed with future firmware, so we'll see...
Final Thoughts
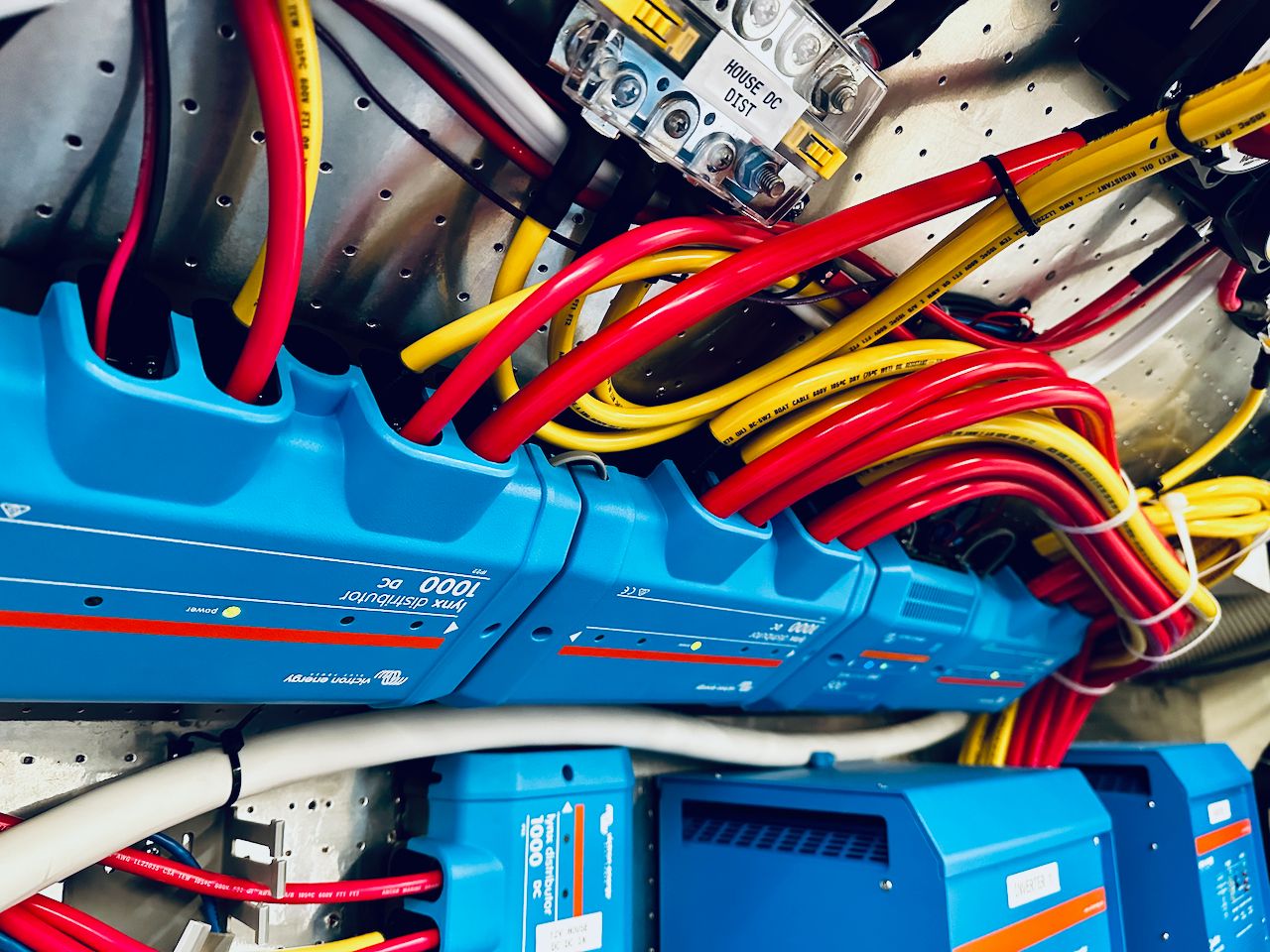
The new power system has been amazingly reliable, easy to see all of the data and status, and provides a wonderful amount of capacity that allows us to be quietly at anchor for multiple days. Simplifying the AC panel down to one 120 volt AC input and putting everything on inverter has really made my job as captain a lot easier when it comes to dealing with power, and it means crew and guests have an easier time as well. There are still some refinements to deal with, and some small challenges to overcome, but that's what I love about working on boating systems - iterative design and continuous improvement. After all, this is version 1 of Kaos system - who knows what will be in version 2!